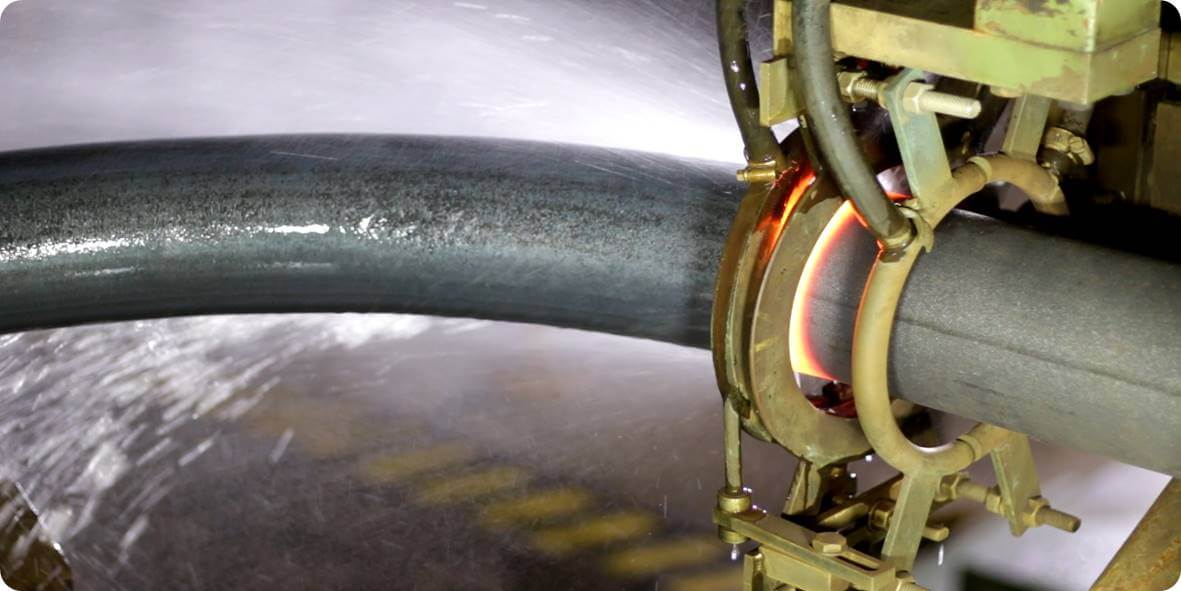
Investigation into the Springback of Pipe Bending Using Induction Heating
Introduction
Pipe bending is a critical process in industries such as construction, oil and gas, power generation, and transportation. It allows for the creation of custom pipe geometries that meet specific design and operational requirements. However, one of the most significant challenges in pipe bending is springback, a phenomenon where the pipe tends to return partially to its original shape after bending due to the elastic recovery of the material.
When using induction heating for pipe bending, springback behavior becomes even more complex due to the localized heating and the resulting thermal gradients. Understanding and controlling springback is essential to ensure the precision and reliability of the final product. This article investigates the factors influencing springback during induction heating pipe bending, methods to predict and mitigate springback, and its implications for industrial applications.
What is Springback in Pipe Bending?
Springback is the elastic recovery of a material after the bending force is removed. During the bending process, the pipe undergoes both elastic deformation (temporary) and plastic deformation (permanent). Once the bending force is removed, the elastic portion of the deformation causes the pipe to partially return to its original shape, resulting in a deviation from the intended bend angle.
Key Characteristics of Springback:
- Magnitude: The degree of springback depends on the material properties, bending radius, and process parameters.
- Direction: Springback typically reduces the bend angle, requiring compensation during the bending process.
- Impact: Uncontrolled springback can lead to dimensional inaccuracies, requiring rework or adjustments.
Induction Heating and Its Role in Pipe Bending
Induction heating is a highly controlled process that uses electromagnetic induction to heat a localized section of the pipe. The heated section becomes more ductile, allowing for easier bending with reduced force. Induction heating is widely used for pipe bending due to its precision, efficiency, and ability to handle large-diameter pipes.
Advantages of Induction Heating in Pipe Bending:
- Localized Heating: Only the bending area is heated, minimizing thermal stress in the rest of the pipe.
- Reduced Force: Heating softens the material, requiring less mechanical force for bending.
- Improved Accuracy: The process allows for tight control over the bend radius and angle.
- Wide Material Compatibility: Suitable for various materials, including carbon steel, stainless steel, and alloy steel.
However, the thermal gradients introduced by induction heating can influence the material’s elastic recovery behavior, making springback prediction more challenging.
Factors Influencing Springback in Induction Heating Pipe Bending
Springback is influenced by a combination of material properties, geometric factors, and process parameters. Below is an in-depth analysis of these factors:
1. Material Properties
- Elastic Modulus:
- Materials with a higher elastic modulus (e.g., stainless steel) exhibit greater springback.
- Yield Strength:
- Higher yield strength materials resist plastic deformation, leading to increased springback.
- Thermal Conductivity:
- Materials with low thermal conductivity retain heat longer, affecting the distribution of thermal gradients and springback behavior.
2. Geometric Factors
- Pipe Diameter (D):
- Larger-diameter pipes tend to exhibit less springback due to their increased stiffness.
- Wall Thickness (t):
- Thicker-walled pipes experience less springback as they are more resistant to elastic recovery.
- Bend Radius (R):
- Tighter bend radii result in higher springback due to increased elastic strain.
3. Process Parameters
- Heating Temperature:
- Higher temperatures reduce the material’s yield strength, increasing plastic deformation and reducing springback.
- Heating Zone Width:
- A wider heating zone creates a more uniform thermal gradient, minimizing springback.
- Cooling Rate:
- Rapid cooling can induce residual stresses, affecting springback behavior.
- Bending Speed:
- Faster bending speeds can lead to uneven heating and increased springback.
4. Residual Stresses
Residual stresses introduced during the bending process can contribute to springback. These stresses are influenced by:
- The heating and cooling cycle.
- The material’s response to thermal and mechanical loading.
Experimental Investigation of Springback in Induction Heating Pipe Bending
To better understand springback behavior, an experimental study was conducted on pipes bent using the induction heating process. The study focused on the effects of material properties, geometric factors, and process parameters on springback magnitude.
Experimental Setup
- Pipe Material: Carbon steel (ASTM A106 Grade B) and stainless steel (AISI 304).
- Pipe Dimensions:
- Outer diameter: 100 mm.
- Wall thickness: 8 mm.
- Bending Radius: 3D (three times the pipe diameter).
- Induction Heating Parameters:
- Heating temperature: 900°C.
- Heating zone width: 50 mm.
- Cooling method: Water jet cooling.
Results and Observations
Parameter | Carbon Steel | Stainless Steel |
---|---|---|
Springback Angle (°) | 2.5 | 4.0 |
Elastic Modulus (GPa) | 200 | 210 |
Yield Strength (MPa) | 250 | 300 |
Thermal Conductivity (W/m·K) | 50 | 16 |
Key Findings:
- Material Influence:
- Stainless steel exhibited higher springback due to its higher elastic modulus and yield strength.
- Geometric Influence:
- Thicker-walled pipes showed reduced springback compared to thinner-walled pipes.
- Process Influence:
- Higher heating temperatures reduced springback by increasing plastic deformation.
- Faster cooling rates led to higher residual stresses, increasing springback.
Methods to Predict and Mitigate Springback
1. Springback Prediction Models
Accurate prediction of springback is essential for compensating during the bending process. Common prediction methods include:
- Analytical Models:
- Based on material properties, bending radius, and wall thickness.
- Example: The elastic-plastic bending theory calculates springback using the relationship between elastic and plastic strain.
- Finite Element Analysis (FEA):
- Simulates the bending process, including thermal and mechanical effects.
- Provides detailed insights into springback behavior for complex geometries.
2. Springback Compensation
To mitigate springback, the following strategies can be employed:
- Overbending:
- The pipe is bent beyond the desired angle to compensate for springback.
- Optimized Heating Parameters:
- Higher heating temperatures and wider heating zones reduce springback by promoting plastic deformation.
- Controlled Cooling:
- Gradual cooling minimizes residual stresses, reducing springback.
- Material Selection:
- Using materials with lower elastic modulus and yield strength can reduce springback.
Applications of Induction Heating Pipe Bending with Springback Control
Springback control is critical in industries where precision and reliability are paramount. Key applications include:
1. Power Generation
- High-pressure steam and water pipes in power plants require precise bends to ensure efficient operation and safety.
2. Oil and Gas
- Pipeline systems for transporting oil and gas over long distances rely on accurate bends to minimize pressure losses.
3. Automotive and Aerospace
- Exhaust systems and structural components require tight tolerances to meet performance and safety standards.
4. Construction
- Structural steel pipes used in bridges and buildings must meet strict dimensional requirements.
Challenges in Springback Control
Despite advancements in prediction and compensation methods, springback control remains challenging due to:
- Material Variability:
- Inconsistent material properties can lead to unpredictable springback behavior.
- Thermal Gradients:
- Uneven heating and cooling can introduce residual stresses, complicating springback prediction.
- Complex Geometries:
- Pipes with non-uniform cross-sections or multi-plane bends are more difficult to model and control.
- Process Limitations:
- Achieving the optimal balance between heating, bending, and cooling parameters requires precise control and expertise.
Future Trends in Springback Research
As industries demand higher precision and efficiency, research into springback behavior is expected to focus on the following areas:
1. Advanced Simulation Tools
- Development of more accurate FEA models that account for thermal, mechanical, and microstructural effects.
2. Material Innovations
- Exploration of new materials and coatings with reduced elastic recovery properties.
3. Automation and AI
- Integration of machine learning algorithms to predict and compensate for springback in real-time.
4. In-Situ Monitoring
- Use of sensors and cameras to monitor the bending process and adjust parameters dynamically.
Conclusion
Springback is a critical factor in the precision and reliability of pipe bending using induction heating. By understanding the factors influencing springback and employing advanced prediction and compensation methods, manufacturers can achieve tighter tolerances and improved product quality.
The combination of induction heating and springback control offers a powerful solution for producing high-quality pipe bends in industries such as power generation, oil and gas, and construction. As technology advances, the ability to predict and mitigate springback will continue to improve, enabling more efficient and sustainable manufacturing processes.
You must be logged in to post a comment.