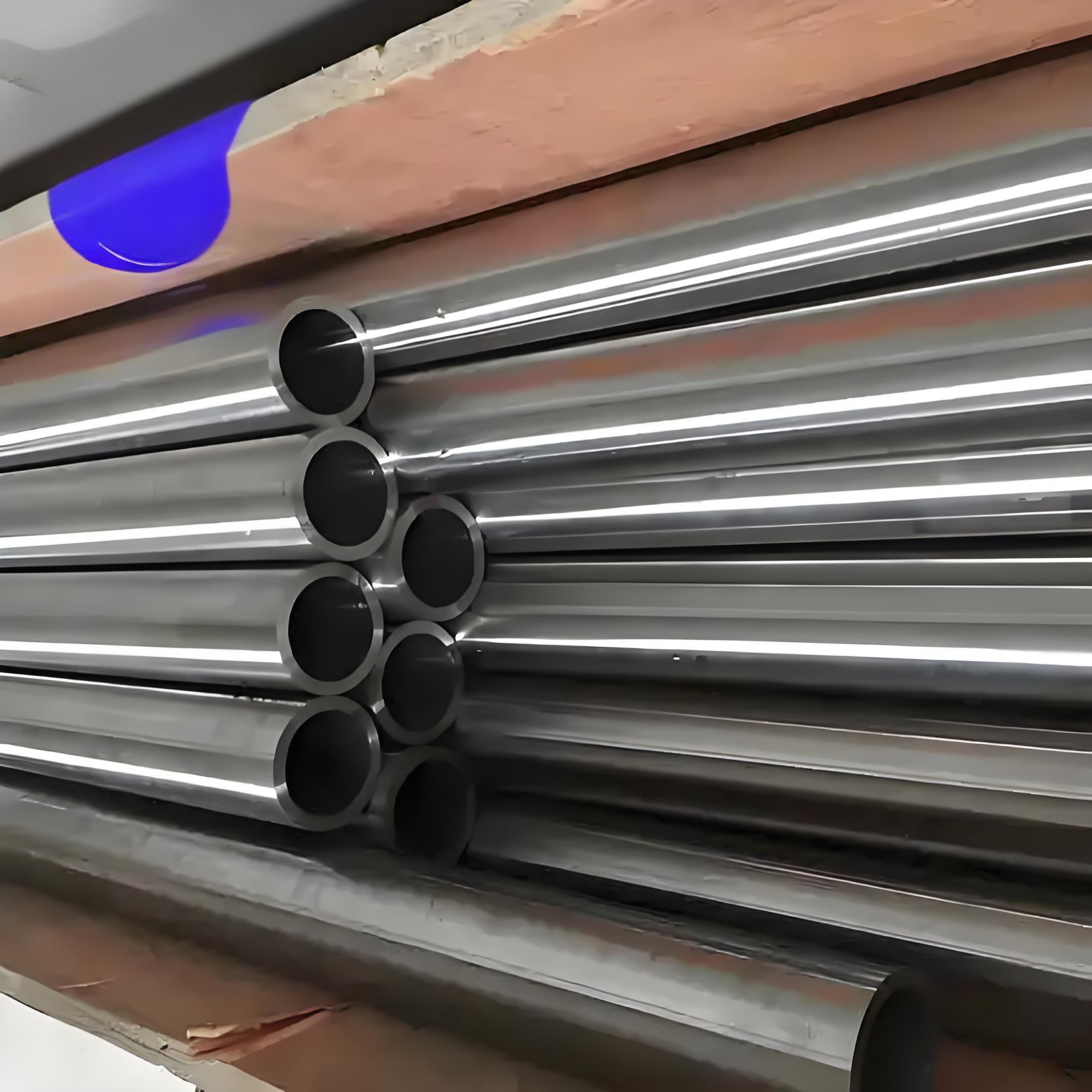
Hastelloy® X Alloy Pipe (UNS N06002): Comprehensive Overview
Hastelloy® X is a nickel-chromium-iron-molybdenum superalloy developed by Haynes International, Inc. for exceptional high-temperature strength, oxidation resistance, and corrosion resistance in extreme environments. Designated as UNS N06002, Hastelloy® X is widely used in seamless and welded pipes and tubes for applications in aerospace, chemical processing, petrochemical industries, and power generation. Its versatility, formability, and weldability make it a preferred material for components like gas turbine combustors, industrial furnace parts, and chemical processing equipment.
This section provides a detailed exploration of Hastelloy® X alloy pipe, including its specifications, chemical composition, physical and mechanical properties, applications, and frequently asked questions (FAQs). Tables are used to present parameters clearly, ensuring a structured and accessible format.
1. Description of Hastelloy® X Alloy Pipe (UNS N06002)
Hastelloy® X (UNS N06002) is a solid-solution-strengthened nickel-based superalloy designed for high-temperature and corrosive environments. It combines high strength, excellent oxidation resistance up to 2200°F (1200°C), and good resistance to stress corrosion cracking, carburization, and nitriding. The alloy’s balanced composition of nickel, chromium, iron, and molybdenum provides durability in both oxidizing and reducing atmospheres, making it ideal for pipes and tubes in demanding applications.
Key Features:
-
High-Temperature Performance: Maintains strength and structural integrity at elevated temperatures, suitable for gas turbines and industrial furnaces.
-
Corrosion Resistance: Resists oxidation, chloride-induced stress corrosion cracking, and pitting in aggressive chemical environments.
-
Fabrication Ease: Excellent formability and weldability, allowing for complex pipe and tube configurations.
-
Versatility: Used in seamless and welded forms for pipes, tubes, and fittings in aerospace, chemical, and energy sectors.
Hastelloy® X pipes are available in various forms, including seamless pipes, welded pipes, and tubing, meeting standards like ASTM B622 (seamless) and ASTM B619/B626 (welded). The alloy’s ability to withstand thermal cycling and mechanical stress makes it a go-to material for critical applications.
2. Specifications of Hastelloy® X Alloy Pipe
Hastelloy® X pipes and tubes are manufactured to precise industry standards to ensure performance in high-temperature and corrosive environments. Below is a table summarizing the key specifications for Hastelloy® X (UNS N06002) pipes and tubes, followed by a detailed explanation.
Table 1: Specifications for Hastelloy® X Alloy Pipe (UNS N06002)
Parameter
|
Details
|
---|---|
Alloy Designation
|
Hastelloy® X (UNS N06002)
|
Common Standards
|
ASTM B622 (Seamless Pipe/Tube), ASTM B619/B626 (Welded Pipe/Tube), ASME SB-622, AMS 5587
|
Pipe Types
|
Seamless, Welded, ERW (Electric Resistance Welded), Fabricated
|
Tube Types
|
Seamless, Welded, U-Tubes, Capillary Tubes
|
Size Range
|
– Outer Diameter (OD): 1/8″ to 48″ (3.175 mm to 1219 mm)
– Wall Thickness: SCH 5, 10, 40, 80, 160, XXS
– Length: Up to 12 meters (custom lengths available)
|
Surface Finish
|
Annealed, Pickled, Polished, Mill Finish
|
Forms
|
Round, Square, Rectangular, Hydraulic, Coiled Tubes
|
Testing
|
Hydrostatic, Eddy Current, Flattening, Flaring, Tensile, Hardness
|
Certifications
|
ISO 9001, ASME, ASTM, EN 10204 3.1/3.2
|
Welding Methods
|
GTAW (TIG), GMAW (MIG), SMAW, Resistance Welding
|
Heat Treatment
|
Solution Annealed at 2150°F (1177°C), followed by rapid cooling
|
Detailed Explanation:
-
Standards: ASTM B622 governs seamless Hastelloy® X pipes and tubes, ensuring uniformity in dimensions and mechanical properties. ASTM B619/B626 applies to welded pipes, with B626 specifically for tubing. AMS 5587 is used for aerospace applications, ensuring high-temperature performance.
-
Size and Forms: Pipes are available in a wide range of diameters and wall thicknesses (e.g., Schedule 40, 80) to suit applications from small-diameter tubing in heat exchangers to large-diameter piping in chemical plants. Custom lengths and shapes (e.g., U-tubes for heat exchangers) are also offered by suppliers like Mega Mex and NeoNickel.
-
Testing: Pipes undergo rigorous non-destructive testing (e.g., eddy current, hydrostatic) to ensure defect-free performance under pressure and temperature.
-
Heat Treatment: Solution annealing enhances corrosion resistance and ductility, critical for pipes exposed to thermal cycling.
Suppliers like Magellan Metals, American Special Metals, and High Performance Alloys provide Hastelloy® X pipes meeting these specifications, with customization options for specific project needs.
3. Applications of Hastelloy® X Alloy Pipe
Hastelloy® X pipes and tubes are used in industries requiring materials that withstand extreme temperatures, corrosive media, and mechanical stress. Below is a table summarizing key applications, followed by a detailed discussion.
Table 2: Applications of Hastelloy® X Alloy Pipe (UNS N06002)
Industry
|
Applications
|
---|---|
Aerospace
|
Gas turbine combustor cans, flame holders, transition ducts, afterburners, tailpipes
|
Chemical Processing
|
Piping systems, heat exchangers, reaction vessels, distillation columns
|
Petrochemical
|
Refinery piping, flare stacks, sulfur recovery units
|
Power Generation
|
Boiler tubes, superheater tubes, flue gas desulfurization systems
|
Industrial Furnaces
|
Retorts, muffles, radiant tubes, heat treatment equipment
|
Nuclear
|
High-temperature components in experimental reactors
|
Detailed Discussion:
-
Aerospace: Hastelloy® X is a staple in gas turbine engines due to its ability to maintain strength and resist oxidation at temperatures up to 2200°F (1200°C). Pipes and tubes are used in combustor cans, flame holders, and afterburners, where thermal fatigue resistance is critical. For example, transition ducts in jet engines rely on Hastelloy® X for durability under cyclic heating and cooling.
-
Chemical Processing: The alloy’s resistance to oxidizing and reducing environments makes it ideal for piping systems handling acids (e.g., sulfuric, nitric) and chlorides. Heat exchangers and reaction vessels benefit from its corrosion resistance and weldability.
-
Petrochemical: In refineries, Hastelloy® X pipes are used in sulfur recovery units and flare stacks, where high temperatures and corrosive gases (e.g., H2S) are present. The alloy’s resistance to carburization and nitriding ensures longevity.
-
Power Generation: Boiler and superheater tubes in coal-fired or gas-fired power plants use Hastelloy® X for its high-temperature strength and resistance to flue gas corrosion.
-
Industrial Furnaces: Radiant tubes and muffles in heat treatment furnaces leverage the alloy’s oxidation resistance and thermal stability.
-
Nuclear: While less common, Hastelloy® X is used in experimental high-temperature reactors due to its stability in extreme conditions.
The alloy’s versatility ensures its use in both seamless pipes for high-pressure applications and welded pipes for cost-effective, large-diameter systems.
4. Chemical Composition of Hastelloy® X Alloy
The chemical composition of Hastelloy® X is carefully balanced to achieve its high-temperature and corrosion-resistant properties. Below is a table detailing the composition, followed by an explanation of each element’s role.
Table 3: Chemical Composition of Hastelloy® X (UNS N06002)
Element
|
Weight %
|
---|---|
Nickel (Ni)
|
Balance (47–52%)
|
Chromium (Cr)
|
20.5–23.0
|
Iron (Fe)
|
17.0–20.0
|
Molybdenum (Mo)
|
8.0–10.0
|
Cobalt (Co)
|
0.5–2.5
|
Tungsten (W)
|
0.2–1.0
|
Manganese (Mn)
|
1.0 max
|
Silicon (Si)
|
1.0 max
|
Carbon (C)
|
0.05–0.15
|
Phosphorus (P)
|
0.04 max
|
Sulfur (S)
|
0.03 max
|
Aluminum (Al)
|
0.5 max
|
Titanium (Ti)
|
0.15 max
|
Boron (B)
|
0.008 max
|
Role of Key Elements:
-
Nickel (Ni): Forms the matrix, providing corrosion resistance and high-temperature stability. The high nickel content ensures ductility and weldability.
-
Chromium (Cr): Enhances oxidation resistance and forms a protective oxide layer at high temperatures, critical for furnace and turbine applications.
-
Iron (Fe): Improves strength and reduces cost while maintaining corrosion resistance.
-
Molybdenum (Mo): Increases resistance to pitting and crevice corrosion, especially in chloride-rich environments, and enhances high-temperature strength.
-
Cobalt (Co): Improves high-temperature strength and creep resistance.
-
Tungsten (W): Contributes to solid-solution strengthening, enhancing mechanical properties at elevated temperatures.
-
Carbon (C): Controlled to minimize carbide precipitation during welding, ensuring corrosion resistance in the heat-affected zone.
The precise composition, as specified by ASTM and AMS standards, ensures consistent performance across applications.
5. Physical Properties of Hastelloy® X Alloy
The physical properties of Hastelloy® X determine its suitability for high-temperature and corrosive environments. Below is a table summarizing key physical properties, followed by a discussion.
Table 4: Physical Properties of Hastelloy® X (UNS N06002)
Property
|
Value
|
---|---|
Density
|
8.22 g/cm³ (0.297 lb/in³)
|
Melting Range
|
2300–2470°F (1260–1355°C)
|
Thermal Conductivity
|
11.6 W/m·K at 100°C (8.0 BTU/ft·h·°F)
|
Specific Heat Capacity
|
486 J/kg·K at 20°C (0.116 BTU/lb·°F)
|
Electrical Resistivity
|
1.18 µΩ·m at 20°C
|
Coefficient of Thermal Expansion
|
13.3 µm/m·°C at 20–1000°C (7.4 µin/in·°F)
|
Modulus of Elasticity
|
205 GPa (29.7 × 10⁶ psi) at 20°C
|
Discussion:
-
Density: The moderate density of 8.22 g/cm³ makes Hastelloy® X suitable for lightweight yet strong components in aerospace applications.
-
Melting Range: The high melting range (1260–1355°C) ensures structural integrity in extreme heat, such as in gas turbine combustors.
-
Thermal Conductivity: Low thermal conductivity (11.6 W/m·K) helps retain heat in furnace components but requires careful design in heat exchangers.
-
Thermal Expansion: The coefficient of 13.3 µm/m·°C is moderate, reducing thermal stress in pipes during thermal cycling.
-
Elastic Modulus: The high modulus (205 GPa) indicates stiffness, ensuring dimensional stability under mechanical loads.
These properties make Hastelloy® X pipes ideal for applications requiring thermal stability and resistance to deformation.
6. Mechanical Properties of Hastelloy® X Alloy
The mechanical properties of Hastelloy® X ensure its performance under high stress and temperature. Below is a table summarizing key properties, followed by an explanation.
Table 5: Mechanical Properties of Hastelloy® X (UNS N06002)
Property
|
Value (Annealed Condition)
|
---|---|
Tensile Strength (Ultimate)
|
725 MPa (105 ksi) min
|
Yield Strength (0.2% Offset)
|
310 MPa (45 ksi) min
|
Elongation
|
35% min
|
Hardness
|
241 HB max (Brinell)
|
Creep Strength
|
48 MPa at 1500°F (816°C) for 10,000 hours
|
Fatigue Strength
|
~300 MPa at 10⁷ cycles (room temperature)
|
Impact Toughness
|
Good, retains ductility at low temperatures
|
Temperature-Dependent Properties (Approximate):
Temperature
|
Tensile Strength
|
Yield Strength
|
Elongation
|
---|---|---|---|
20°C (68°F)
|
755 MPa (110 ksi)
|
345 MPa (50 ksi)
|
40%
|
1000°C (1832°F)
|
290 MPa (42 ksi)
|
165 MPa (24 ksi)
|
50%
|
Discussion:
-
Tensile and Yield Strength: Hastelloy® X offers high tensile strength (725 MPa) and yield strength (310 MPa) in the annealed condition, suitable for high-pressure piping systems. Strength decreases at higher temperatures but remains sufficient for applications up to 1200°C.
-
Elongation: The high elongation (35–50%) indicates excellent ductility, allowing pipes to be formed into complex shapes and withstand thermal expansion.
-
Creep Resistance: The alloy’s creep strength (48 MPa at 1500°F for 10,000 hours) ensures long-term performance in furnaces and turbines.
-
Fatigue Resistance: Good fatigue strength (~300 MPa) supports cyclic loading in aerospace components like combustor cans.
-
Hardness: Moderate hardness (241 HB) facilitates machining while maintaining wear resistance.
These properties make Hastelloy® X pipes reliable for both static and dynamic loads in extreme conditions.
7. Hastelloy® X Tube/Pipe FAQs
Below are frequently asked questions about Hastelloy® X alloy pipes and tubes, addressing common concerns and providing practical insights.
FAQ 1: What makes Hastelloy® X suitable for high-temperature applications?
Answer: Hastelloy® X’s high nickel, chromium, and molybdenum content provides exceptional oxidation resistance and strength up to 2200°F (1200°C). Its solid-solution strengthening and resistance to carburization and nitriding ensure durability in gas turbines, furnaces, and chemical reactors.
FAQ 2: Can Hastelloy® X pipes be welded, and what precautions are needed?
Answer: Yes, Hastelloy® X is highly weldable using GTAW (TIG), GMAW (MIG), SMAW, or resistance welding. Precautions include:
-
Using matching filler metals (e.g., Hastelloy® X or INCONEL® 617).
-
Avoiding submerged arc welding to prevent hot cracking.
-
Ensuring clean surfaces to prevent contamination.
-
Post-weld heat treatment (if required) to relieve residual stresses.
FAQ 3: How does Hastelloy® X compare to other nickel alloys like Inconel® 718?
Answer: Compared to Inconel® 718, Hastelloy® X offers:
-
Better oxidation resistance at higher temperatures (up to 2200°F vs. 1800°F for 718).
-
Superior formability and weldability due to solid-solution strengthening (vs. precipitation hardening in 718).
-
Slightly lower strength at intermediate temperatures but better creep resistance above 1500°F. Hastelloy® X is preferred for furnace and turbine components, while Inconel® 718 is used in high-strength aerospace parts.
FAQ 4: What are the corrosion resistance properties of Hastelloy® X pipes?
Answer: Hastelloy® X resists:
-
Oxidation in air up to 2200°F (1200°C).
-
Chloride-induced stress corrosion cracking in petrochemical environments.
-
Carburizing and nitriding atmospheres in furnaces. However, it is less resistant to highly reducing acids (e.g., hydrochloric) compared to Hastelloy® C-276.
FAQ 5: What are the typical costs of Hastelloy® X pipes?
Answer: Costs vary based on size, form (seamless vs. welded), and supplier. Seamless Hastelloy® X pipes are more expensive than welded due to manufacturing complexity. For exact pricing, contact suppliers like abtersteel (abtersteel.com) or Special Metals (pieun.com). The alloy’s durability often offsets initial costs in long-term applications.
FAQ 6: How are Hastelloy® X pipes machined or fabricated?
Answer: Machining requires:
-
Rigid setups and sharp carbide tools to counter work hardening.
-
Low cutting speeds (e.g., 20–30 m/min) and ample coolant.
-
Fabrication involves cold or hot forming (hot forming at 2150°F/1177°C). Suppliers provide pre-formed pipes or custom fabrication services.
FAQ 7: What testing is performed on Hastelloy® X pipes?
Answer: Standard tests include:
-
Hydrostatic testing for pressure integrity.
-
Eddy current testing for surface defects.
-
Flattening and flaring tests for ductility.
-
Chemical and mechanical testing to meet ASTM/AMS standards. Certificates (EN 10204 3.1/3.2) are provided by suppliers.
FAQ 8: Are Hastelloy® X pipes available in custom sizes?
Answer: Yes, suppliers like Magellan Metals and NeoNickel offer custom OD, wall thickness, and lengths. U-tubes and coiled tubes are also available for heat exchangers and specialized applications.
FAQ 9: What are the limitations of Hastelloy® X pipes?
Answer: Limitations include:
-
Moderate resistance to highly reducing acids (e.g., HCl), where Hastelloy® C-276 is preferred.
-
Higher cost compared to stainless steel.
-
Machining challenges due to work hardening, requiring specialized equipment.
FAQ 10: Where can I source Hastelloy® X pipes?
Answer: Reputable suppliers include:
-
abtersteel company : www.abtersteel.com
-
Special Metals: pipeun.com
-
Nickel steel company: avatur.com
8. Additional Considerations for Hastelloy® X Alloy Pipe
Fabrication and Installation
-
Forming: Hastelloy® X pipes can be cold-formed for small bends or hot-formed for complex shapes. Hot forming at 2150°F (1177°C) minimizes cracking.
-
Installation: Proper alignment and support are critical to prevent stress concentration in high-temperature piping systems. Flanges, fittings, and valves in Hastelloy® X are available for seamless integration.
-
Cleaning: Pipes should be cleaned to remove contaminants (e.g., oil, grease) before installation to prevent corrosion or weld imperfections.
Cost-Benefit Analysis
While Hastelloy® X pipes are more expensive than stainless steel or carbon steel, their superior performance in extreme environments reduces maintenance and replacement costs. For example, in gas turbines, the alloy’s longevity under thermal cycling outweighs initial investment.
Environmental and Safety Considerations
-
Sustainability: Hastelloy® X is recyclable, supporting sustainable practices in industries like aerospace and power generation.
-
Safety: The alloy is non-toxic, but machining or welding requires proper ventilation to avoid inhalation of fumes. Safety data sheets (SDS) are available from Haynes International (abtersteel.com).
Comparison with Other Hastelloy® Alloys
-
Vs. Hastelloy® C-276: C-276 offers better corrosion resistance in reducing acids but lower high-temperature strength. X is preferred for thermal applications.
-
Vs. Hastelloy® B-3: B-3 excels in hydrochloric acid environments but lacks the oxidation resistance of X.
-
Vs. Hastelloy® G-30: G-30 is optimized for phosphoric acid, while X is better for high-temperature oxidizing conditions.
9. Conclusion
Hastelloy® X alloy pipe (UNS N06002) is a premier material for high-temperature, corrosive, and mechanically demanding applications. Its balanced composition of nickel, chromium, iron, and molybdenum ensures exceptional performance in aerospace (gas turbines), chemical processing (heat exchangers), petrochemical (refinery piping), and power generation (boiler tubes). The alloy’s high-temperature strength, oxidation resistance, and weldability make it versatile for seamless and welded pipes and tubes, meeting stringent ASTM and AMS standards.
You must be logged in to post a comment.