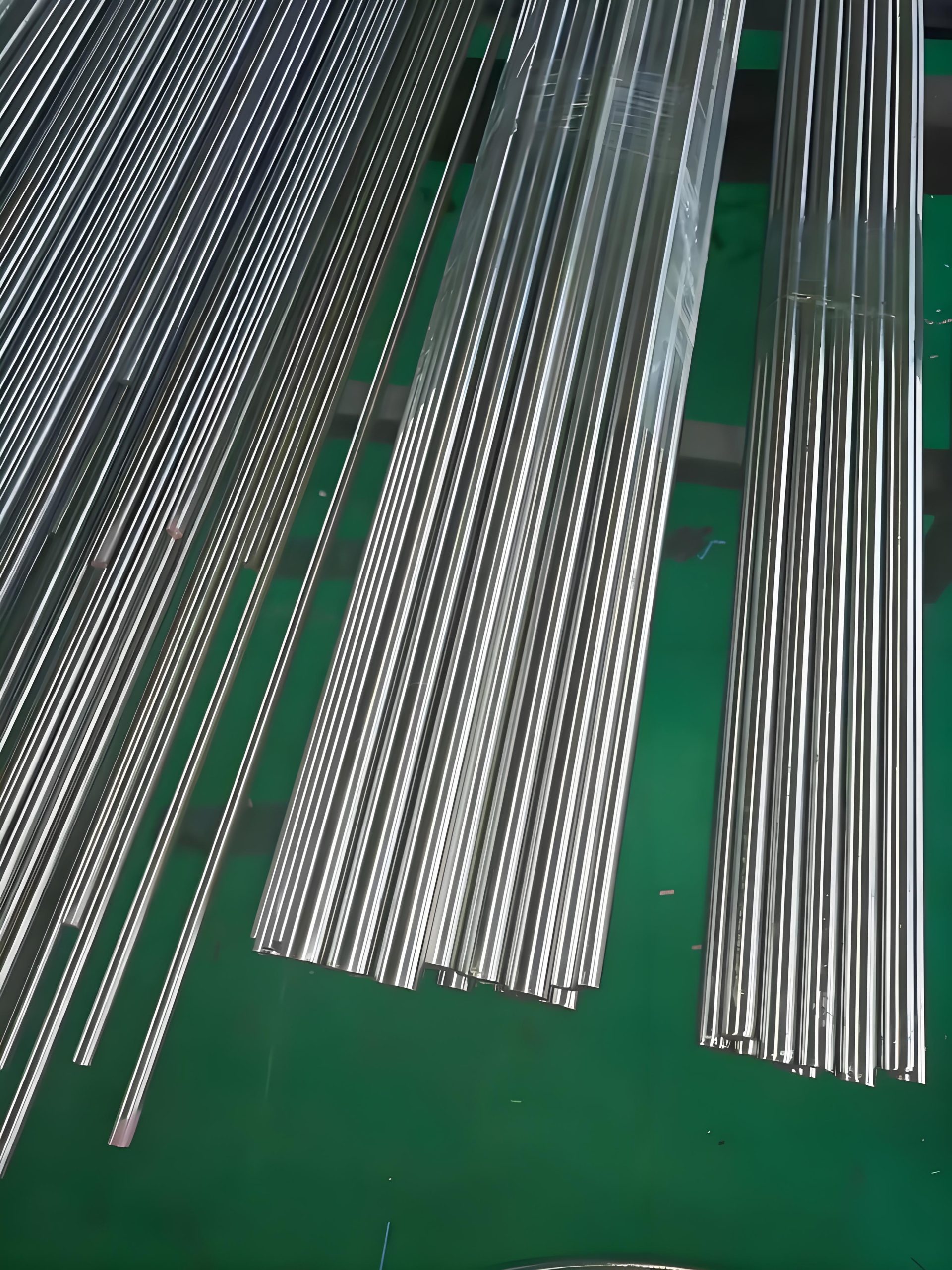
HASTELLOY® X Alloy Overview
Principal Features of HASTELLOY® X Alloy
HASTELLOY® X alloy (UNS N06002, W86002) is a high-performance nickel-chromium-iron-molybdenum superalloy renowned for its exceptional combination of properties, making it a preferred material for demanding applications. This alloy offers outstanding oxidation resistance, high-temperature strength, and fabricability, ensuring reliability in extreme environments. It exhibits remarkable resistance to stress-corrosion cracking in petrochemical applications, maintaining structural integrity under aggressive conditions. Additionally, HASTELLOY® X retains excellent ductility after prolonged exposure to elevated temperatures—1200°F (650°C), 1400°F (760°C), and 1600°F (870°C)—for up to 16,000 hours, making it ideal for long-term service in high-heat environments.
Key attributes include:
- Superior Oxidation Resistance: Performs reliably in oxidizing atmospheres up to 2200°F (1200°C).
- High-Temperature Strength: Maintains mechanical properties under thermal stress, suitable for gas turbines and furnaces.
- Exceptional Fabricability: Easily formed and welded, supporting complex component designs.
- Stress-Corrosion Cracking Resistance: Ensures durability in chloride-rich and petrochemical environments.
These characteristics position HASTELLOY® X as a versatile solution for industries requiring robust materials in extreme conditions.
Ease of Fabrication
HASTELLOY® X alloy is distinguished by its excellent forming and welding characteristics, enabling versatile fabrication for a wide range of applications. The alloy can be hot-worked or forged at a temperature of 2150°F (1177°C), provided the entire workpiece is uniformly heated to ensure consistent properties. Its inherent ductility also allows for cold-working, facilitating the creation of intricate shapes and components without compromising material integrity.
To optimize performance, all hot- or cold-worked parts should undergo annealing followed by rapid cooling. This process restores the alloy’s optimal balance of strength, ductility, and corrosion resistance, ensuring long-term reliability.
Welding is a key strength of HASTELLOY® X, as it can be joined using multiple techniques, including:
- Gas Tungsten Arc Welding (GTAW/TIG): Provides precise, high-quality welds for critical components.
- Gas Metal Arc Welding (GMAW/MIG): Suitable for high-speed production.
- Shielded Metal Arc Welding (SMAW): Offers flexibility for field applications.
- Resistance Welding: Ideal for thin sections and specialized assemblies.
To ensure weld integrity, use matching filler metals (e.g., HASTELLOY® X or INCONEL® 617) and maintain clean surfaces to prevent contamination. Avoid submerged arc welding to minimize the risk of hot cracking.
For detailed fabrication guidelines, including recommended tools, parameters, and best practices, refer to the technical resources provided by Abtersteel.com.
Heat Treatment
HASTELLOY® X alloy is typically supplied in the solution heat-treated condition unless otherwise specified, ensuring optimal performance for most applications. The standard heat treatment involves solution annealing at 2150°F (1177°C) followed by rapid cooling to lock in the alloy’s microstructure and enhance its corrosion resistance and ductility. For bright annealed products, cooling is performed in a hydrogen atmosphere to maintain surface quality and prevent oxidation.
Important Considerations:
- Annealing at temperatures below 2150°F (1177°C) may lead to the precipitation of secondary phases, such as carbides or intermetallic compounds, which can reduce the alloy’s strength and ductility.
- Rapid cooling after heat treatment is critical to prevent phase transformations that could compromise performance.
Proper heat treatment ensures that HASTELLOY® X pipes, tubes, and components deliver consistent mechanical properties and resistance to environmental degradation, making them suitable for high-stakes applications in aerospace, chemical processing, and industrial furnaces.
Applications in Aerospace, Furnaces, and Chemical Processing
HASTELLOY® X alloy is a cornerstone material in industries requiring exceptional performance under extreme temperatures and corrosive conditions. Its unique combination of high-temperature strength, oxidation resistance, and fabricability makes it indispensable for critical components in aerospace, industrial furnaces, and chemical processing.
Industry | Applications |
---|---|
Aerospace | Combustion zone components (transition ducts, combustor cans, spray bars, flame holders), afterburners, tailpipes, cabin heaters |
Industrial Furnaces | Furnace rolls, retorts, muffles, radiant tubes, heat treatment equipment |
Chemical Processing | Retorts, muffles, catalyst support grids, furnace baffles, pyrolysis tubing, flash drier components |
Detailed Applications:
- Aerospace: HASTELLOY® X is extensively used in gas turbine engines for components exposed to extreme heat and thermal cycling. Combustion zone parts, such as transition ducts, combustor cans, spray bars, and flame holders, benefit from the alloy’s ability to withstand temperatures up to 2200°F (1200°C) while resisting oxidation and thermal fatigue. Afterburners, tailpipes, and cabin heaters also leverage its high strength and durability, ensuring reliable performance in jet engines and auxiliary systems.
- Industrial Furnaces: The alloy’s exceptional resistance to oxidizing, reducing, and neutral atmospheres makes it ideal for furnace applications. Furnace rolls made of HASTELLOY® X have demonstrated remarkable longevity, remaining in excellent condition after 8,700 hours of operation at 2150°F (1177°C). Other components, such as retorts, muffles, and radiant tubes, benefit from the alloy’s thermal stability and resistance to carburization and nitriding.
- Chemical Processing: In the chemical process industry, HASTELLOY® X is used for equipment exposed to corrosive media and high temperatures. Components like retorts, catalyst support grids, furnace baffles, pyrolysis tubing, and flash drier components rely on the alloy’s ability to resist chemical attack and maintain structural integrity. Its resistance to stress-corrosion cracking is particularly valuable in environments involving chlorides or acidic compounds.
The alloy’s versatility and proven performance across these industries underscore its value as a high-performance material for critical applications.
You must be logged in to post a comment.