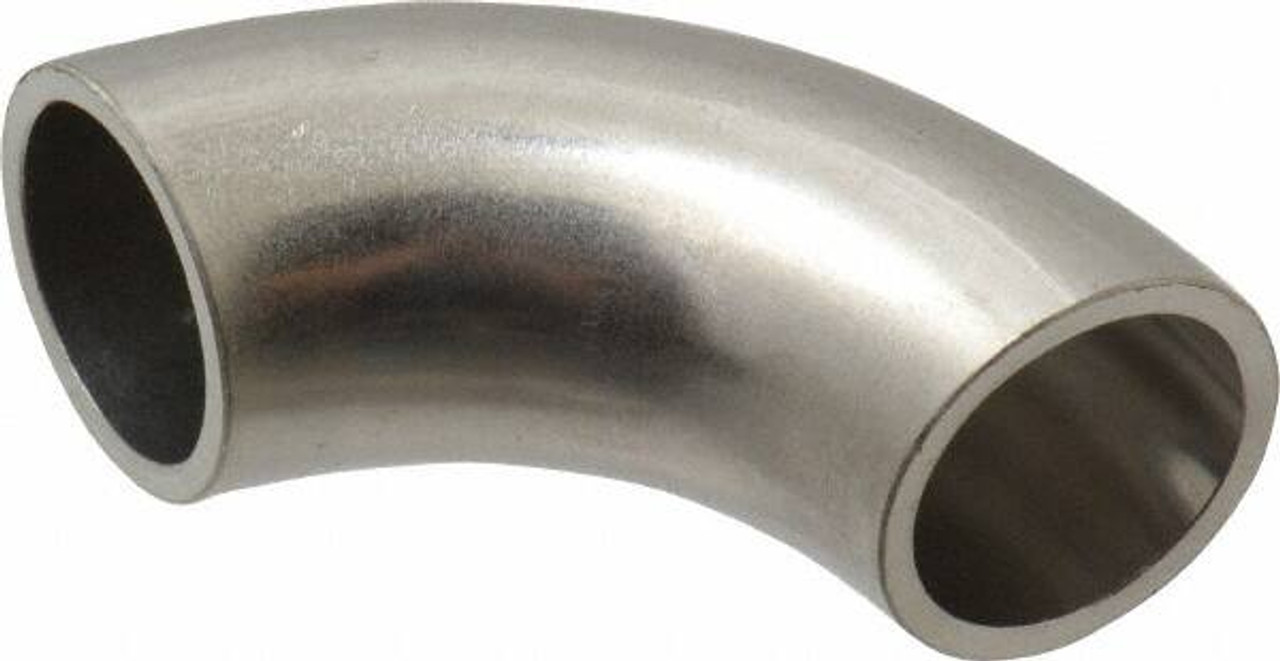
ASME B16.25 الكوع الملحوم بعقب
مقدمة
ASME B16.25 is a standard that covers the preparation of butt-welding ends of piping components to make a welded joint. هذا المعيار أمر بالغ الأهمية لضمان التثبيت المناسب واللحام لمكونات الأنابيب, مما يؤدي إلى مفاصل موثوقة وخالية من التسرب. Butt weld elbows are a common type of fitting covered under this standard, used to change the direction of flow in a piping system by 45°, 90°, or other angles.
Types of Butt Weld Elbows
1. 45-درجة الكوع
The 45-degree elbow changes the direction of the flow by 45°. It is commonly used in systems where a smooth change in direction is needed without causing turbulence.
2. 90-درجة الكوع
The 90-degree elbow changes the direction of the flow by 90°. It is the most commonly used type of elbow in piping systems, ideal for making sharp turns.
3. 180-درجة الكوع
The 180-degree elbow is used to change the direction of flow by 180°, effectively reversing the flow direction. This type is less common but is used in specific situations where a U-turn in the piping is required.
Specifications and Dimensions
1. الاسمي حجم الأنابيب (مصادر القدرة النووية)
ASME B16.25 covers a wide range of nominal pipe sizes (مصادر القدرة النووية), typically from 1/2 بوصة ل 48 بوصة. The size of the elbow correlates with the size of the pipe it will be welded to.
2. سمك الجدار
The wall thickness of butt weld elbows is specified by the schedule number (مثل, SCH 10, SCH 40, SCH 80). The schedule number indicates the thickness of the pipe wall and, بالتالي, the elbow’s wall.
3. Radius of Curvature
There are two main types of elbow curvature:
- نصف قطر قصير (ريال): The radius of curvature is equal to the nominal pipe size (1د).
- نصف قطر طويل (إل آر): نصف قطر الانحناء هو 1.5 أضعاف حجم الأنبوب الاسمي (1.5د). Long radius elbows are commonly used because they cause less pressure drop and flow disruption.
4. End Preparation
The ends of butt weld elbows are prepared according to ASME B16.25 to ensure proper welding. This preparation typically involves beveling the ends of the elbow to facilitate the welding process.
اختيار المواد
Butt weld elbows are manufactured from various materials to suit different applications and environments. وتشمل المواد المشتركة:
- الكربون الصلب: Suitable for general-purpose applications.
- الفولاذ المقاوم للصدأ: Offers excellent corrosion resistance and is used in chemical, pharmaceutical, and food industries.
- خليط معدني: Used in high-pressure and high-temperature environments.
- دوبلكس ستانلس ستيل: Combines the properties of austenitic and ferritic stainless steels, offering high strength and excellent resistance to stress corrosion cracking.
عملية التصنيع
1. تزوير
Butt weld elbows are often manufactured using the forging process, which involves shaping the metal using compressive forces. This process enhances the mechanical properties and grain structure of the material.
2. تشكيل
In the forming process, the metal is bent or shaped into the required elbow configuration. This can be done using methods such as hot forming or cold forming, depending on the material and specifications.
3. المعالجة الحرارية
بعد التشكيل, the elbows may undergo heat treatment processes like annealing or normalizing to relieve internal stresses and enhance mechanical properties.
4. بالقطع
The ends of the elbows are machined to ensure they meet the required dimensions and tolerances specified by ASME B16.25.
5. التفتيش والاختبار
Quality control measures such as dimensional inspection, non-destructive testing (NDT), and pressure testing are conducted to ensure the elbows meet the required standards and specifications.
تطبيقات
Butt weld elbows are used in various industries, بما فيها:
- النفط والغاز: For transporting crude oil, غاز طبيعي, and refined products.
- المعالجة الكيميائية: In systems handling corrosive chemicals and high-temperature fluids.
- توليد الطاقة: In high-pressure and high-temperature steam lines.
- معالجة المياه: For conveying water and wastewater in treatment plants.
- الأدوية: In sanitary piping systems requiring high corrosion resistance and cleanliness.
Installation and Welding
1. تحضير
Proper preparation is essential for successful welding. This includes cleaning the pipe and elbow ends, aligning the components, and ensuring the correct fit-up.
2. تقنيات اللحام
Common welding techniques for butt weld elbows include:
- Tungsten Inert Gas (تيغ) لحام: Offers high precision and quality, suitable for thin-walled and critical applications.
- Metal Inert Gas (أنا) لحام: Provides faster welding speeds and is suitable for thicker sections.
- لحام القوس المعدني المحمي (SMAW): Versatile and widely used, especially in field applications.
3. Post-Weld Inspection
بعد اللحام, the joints are inspected using methods such as radiographic testing (ر.ت) or ultrasonic testing (يوتا) to ensure weld integrity and detect any defects.
Future Trends and Innovations
The landscape of manufacturing and application for ASME B16.25 butt weld elbows is poised for significant advancements. These trends and innovations are driven by the need for enhanced performance, الاستدامة, and integration with modern manufacturing technologies.
Advanced Materials
1. High-Performance Alloys
Advancements in metallurgy are leading to the development of high-performance alloys that offer superior strength, المقاومة للتآكل, والمتانة.
- Superalloys: Nickel-based superalloys are being developed for high-temperature and high-stress applications, such as those found in aerospace and power generation.
- Titanium Alloys: Known for their high strength-to-weight ratio and corrosion resistance, titanium alloys are becoming more prevalent in critical applications.
2. Composite Materials
The use of composite materials in piping systems is emerging, combining metals with other materials like ceramics or polymers to enhance properties such as thermal resistance and weight reduction.
التصنيع المضاف (3د الطباعة)
Additive manufacturing is revolutionizing the production of complex piping components, including butt weld elbows.
- Custom Designs: 3D printing enables the creation of custom, complex geometries that are difficult or impossible to achieve with traditional manufacturing methods.
- Rapid Prototyping: Engineers can quickly prototype and test new designs, reducing development time and costs.
- كفاءة المواد: Additive manufacturing minimizes material waste, promoting sustainability.
Smart Manufacturing and Industry 4.0
صناعة 4.0 principles, including IoT (Internet of Things), big data, and AI (Artificial Intelligence), are transforming the manufacturing landscape.
1. Predictive Maintenance
- Sensors and Monitoring: Real-time monitoring of equipment and processes using sensors helps predict failures and schedule maintenance before breakdowns occur.
- Data Analytics: Big data analytics can optimize production processes, reducing downtime and improving efficiency.
2. Automation and Robotics
- Robotic Welding: Automated welding systems ensure consistent quality and precision, reducing human error and increasing throughput.
- Smart Factories: Integrated systems and robotics enhance flexibility and adaptability in manufacturing processes.
Environmental Sustainability
Sustainability is becoming a key focus in the manufacturing of piping components.
1. Recycling and Circular Economy
- Material Recycling: Emphasizing the recycling of metals to reduce raw material consumption and environmental impact.
- Circular Economy: Designing products for easier disassembly and recycling at the end of their life cycle.
2. Eco-Friendly Processes
- التصنيع الأخضر: Implementing processes that minimize energy consumption and emissions, such as using renewable energy sources.
- Low-Impact Coatings: Developing coatings that protect components without harmful environmental effects.
Advanced Coating Technologies
Innovations in coating technologies are enhancing the performance and lifespan of butt weld elbows.
- Nanocoatings: Ultra-thin coatings that provide superior corrosion resistance, wear resistance, and hydrophobic properties.
- Self-Healing Coatings: Coatings that can automatically repair minor damages, extending the service life of components.
Enhanced Inspection and Testing
Improvements in non-destructive testing (NDT) methods are ensuring higher quality and reliability.
- Advanced Ultrasonic Testing (AUT): High-resolution imaging techniques for detecting flaws and ensuring weld integrity.
- Phased Array Ultrasonics (وصلة): Provides detailed images of welds, allowing for precise defect characterization.
Digital Twins
The concept of digital twins—virtual replicas of physical components—allows for simulation and analysis of performance under various conditions.
- Predictive Analysis: Simulating the behavior of components under different scenarios to predict potential issues and optimize designs.
- Maintenance Optimization: Using digital twins to plan maintenance activities and improve asset management.
استنتاج
ASME B16.25 butt weld elbows play a critical role in the reliability and efficiency of piping systems across various industries. Understanding the specifications, مواد, عمليات التصنيع, and installation techniques is essential for selecting and using these components effectively. By adhering to the standards and best practices outlined in ASME B16.25, engineers and technicians can ensure the safety, أداء, and longevity of their piping systems.The future of ASME B16.25 butt weld elbows is set to be shaped by advancements in materials, manufacturing technologies, and sustainability practices. By embracing these trends and innovations, the industry can enhance the performance, مصداقية, and environmental footprint of piping systems, meeting the evolving demands of modern applications.
This comprehensive guide provides a detailed overview of ASME B16.25 butt weld elbows, covering everything from types and specifications to manufacturing processes and applications.This guide provides an insight into the future trends and innovations in the manufacturing and application of ASME B16.25 butt weld elbows, highlighting how emerging technologies and practices are set to transform the industry.
يجب ان تكون تسجيل الدخول لإضافة تعليق.