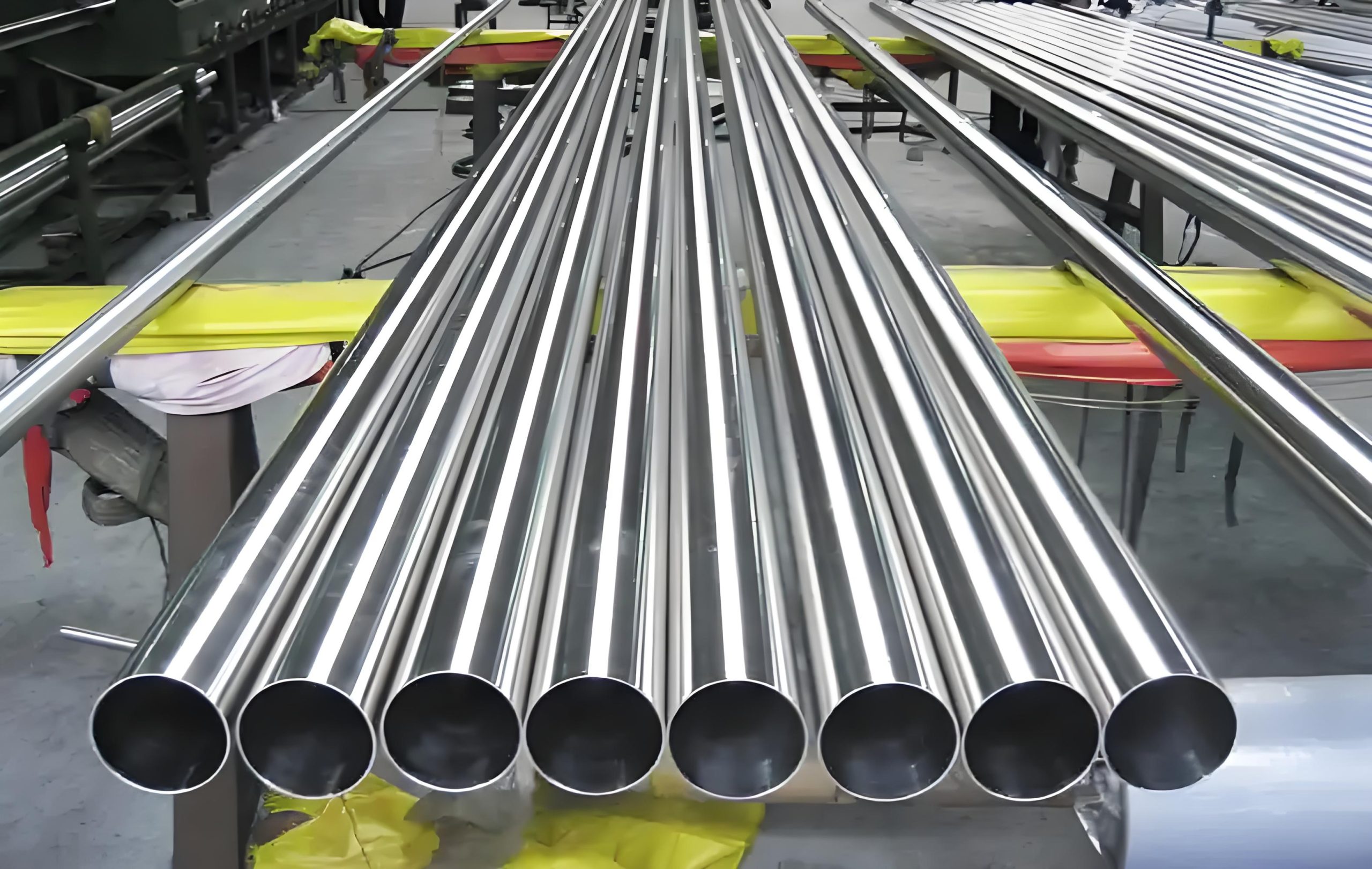
Hastelloy C276 (UNS N10276, W.Nr. 2.4819): Specifications and Applications for Alloy Pipes
Introduction to Hastelloy C276 Alloy Pipes
Hastelloy C276 (UNS N10276, W.Nr. 2.4819) is a nickel-molybdenum-chromium superalloy renowned for its exceptional corrosion resistance in a wide range of aggressive environments. With a composition that includes significant amounts of molybdenum (15-17%), chromium (14.5-16.5%), and tungsten (3-4.5%), this alloy is engineered to withstand harsh conditions involving acids, chlorides, and oxidizing media. Hastelloy C276 pipes, available in seamless and welded forms, are critical components in industries such as chemical processing, petrochemical, marine engineering, and pollution control. These pipes are designed to handle high-pressure fluids, corrosive chemicals, and extreme temperatures, ensuring reliability and safety in demanding applications.
Conforming to standards like ASTM B622 (seamless pipes), ASTM B619 (welded pipes), and ASTM B626 (welded tubing), Hastelloy C276 pipes offer superior performance in environments where stainless steels and other alloys fail. The alloy’s low carbon content minimizes carbide precipitation during welding, making it suitable for as-welded structures without compromising corrosion resistance. This comprehensive analysis explores the chemical composition, mechanical properties, corrosion resistance, manufacturing processes, and applications of Hastelloy C276 pipes, with a comparison to Inconel alloys and other materials, providing valuable insights for engineers and industry professionals.
Chemical Composition and Microstructure
The chemical composition of Hastelloy C276 is carefully balanced to provide exceptional corrosion resistance and mechanical stability. Nickel (balance, ~57%) forms a robust austenitic matrix, offering resistance to reducing environments and chloride-ion stress corrosion cracking (SCC). Molybdenum (15-17%) enhances resistance to pitting and crevice corrosion, while chromium (14.5-16.5%) provides protection against oxidizing media. Tungsten (3-4.5%) further improves corrosion resistance in harsh environments, and low carbon content (≤0.01%) minimizes carbide precipitation during welding. The table below details the chemical composition of Hastelloy C276:
Element | Composition (% by Weight) |
---|---|
Nickel (Ni) | Balance (~57) |
Molybdenum (Mo) | 15.0–17.0 |
Chromium (Cr) | 14.5–16.5 |
Tungsten (W) | 3.0–4.5 |
Iron (Fe) | 4.0–7.0 |
Cobalt (Co) | ≤2.5 |
Manganese (Mn) | ≤1.0 |
Carbon (C) | ≤0.01 |
Silicon (Si) | ≤0.08 |
Phosphorus (P) | ≤0.04 |
Sulfur (S) | ≤0.03 |
Vanadium (V) | ≤0.35 |
The microstructure of Hastelloy C276 is a single-phase, face-centered cubic (FCC) austenitic structure, which provides excellent ductility and toughness. The low carbon content prevents the formation of grain boundary precipitates in the weld heat-affected zone, ensuring corrosion resistance in as-welded conditions. Compared to Inconel 625, which has a similar nickel-chromium-molybdenum composition but lower molybdenum content (~9%), Hastelloy C276 offers superior resistance to reducing acids but slightly less high-temperature strength. The alloy’s microstructure remains stable up to 1040°C, making it suitable for high-temperature applications in chemical processing and power generation.
Mechanical Properties and Heat Treatment
Hastelloy C276 pipes exhibit robust mechanical properties, making them suitable for high-pressure and high-temperature applications. In the annealed condition, the alloy achieves a tensile strength of ≥790 MPa, a yield strength of ≥355 MPa, and an elongation of ≥40%, ensuring excellent ductility. The alloy’s hardness typically ranges from 85-95 HRB, providing a balance of strength and workability. Hastelloy C276 maintains its mechanical integrity from cryogenic temperatures (-196°C) to 1040°C, though prolonged exposure above 870°C may lead to phase instability. The table below summarizes the mechanical properties of Hastelloy C276 pipes:
Property | Value (Annealed Condition) |
---|---|
Tensile Strength (MPa) | ≥790 |
Yield Strength (MPa) | ≥355 |
Elongation (%) | ≥40 |
Hardness (HRB) | 85–95 |
Density (g/cm³) | 8.89 |
Melting Point (°C) | 1325–1370 |
Hastelloy C276 pipes are typically supplied in the annealed condition, with solution annealing at 1120-1180°C followed by rapid quenching to prevent carbide precipitation. Unlike precipitation-hardened alloys like Monel 502, Hastelloy C276 relies on solid-solution strengthening, eliminating the need for post-weld heat treatment in most cases. Compared to Inconel 625 (tensile strength ≥827 MPa), Hastelloy C276 offers similar strength but superior corrosion resistance in reducing environments. Stainless steel 316, with a tensile strength of ≥515 MPa, is less robust and more susceptible to chloride SCC. The alloy’s excellent fabricability allows for cold working and welding without compromising its properties, making it ideal for complex piping systems.
Corrosion Resistance and Environmental Performance
Hastelloy C276 is renowned for its exceptional corrosion resistance, particularly in reducing and oxidizing environments. The high molybdenum content provides outstanding resistance to pitting and crevice corrosion, with corrosion rates as low as 0.01 mm/year in 5% hydrochloric acid (de-aerated). Chromium enhances resistance to oxidizing media, such as nitric acid, with corrosion rates of ~0.05 mm/year in 10% HNO₃. The addition of tungsten further improves performance in harsh environments, including seawater, where the alloy exhibits negligible pitting after three years of exposure. The alloy’s resistance to chloride-ion SCC makes it a preferred choice for marine and chemical processing applications, where stainless steels like 304 and 316 fail.
In tests conducted in 3.5% NaCl solutions, Hastelloy C276 showed pit depths of <0.01 mm, compared to 0.03 mm for 316L stainless steel. Its performance in sulfuric acid (up to 50% concentration) is superior to Monel 400 (~0.1 mm/year), though Inconel 625 performs better in highly oxidizing conditions due to its higher chromium content. Hastelloy C276’s low carbon content minimizes grain boundary precipitation, ensuring corrosion resistance in as-welded structures. Surface treatments like pickling and electropolishing further enhance its performance, particularly in pharmaceutical and food processing applications where high-purity environments are critical. The alloy’s versatility makes it suitable for flue gas desulfurization systems, sour gas wells, and organic chloride processing [Web ID: 6, 7].
Manufacturing and Fabrication
Hastelloy C276 pipes are manufactured to standards such as ASTM B622 (seamless), ASTM B619 (welded), and ASTM B626 (welded tubing). Seamless pipes, produced via extrusion or cold drawing, range from 1/2 inch to 24 inches in diameter, with wall thicknesses from Schedule 5 to XXS. Welded pipes, including ERW and EFW types, can reach diameters up to 48 inches, suitable for large-scale applications like petrochemical pipelines. The alloy’s excellent fabricability allows for welding using GTAW, GMAW, or SMAW, with minimal risk of weld decay due to low carbon content. Machining, however, is challenging due to work-hardening, requiring sharp tools and slow cutting speeds (10-20 m/min) to minimize tool wear.
Flanges, conforming to ASTM B564 and ASME B16.5, are forged or machined from plates, available in types like weld neck, slip-on, and blind, with pressure ratings from 150 to 2500. Annealing at 1120-1180°C followed by rapid quenching ensures optimal corrosion resistance and mechanical properties. Compared to Inconel 625, Hastelloy C276 is slightly harder to machine but offers better corrosion resistance in reducing environments. Surface finishes, such as pickled or polished, enhance corrosion resistance and aesthetics, particularly for flanges in marine applications. The alloy’s compliance with NACE MR0175/ISO 15156 ensures suitability for sour gas environments, making it a preferred choice for oil and gas pipelines [Web ID: 13, 15].
Product Details: Hastelloy C276 Pipes
Hastelloy C276 pipes are available in seamless and welded configurations, designed for high-pressure and corrosive applications. Seamless pipes, per ASTM B622, range from 1/2 inch to 24 inches in diameter, with wall thicknesses from 0.5 mm to 20 mm (Schedules 5 to 160). Welded pipes, per ASTM B619, can reach up to 48 inches, suitable for large-scale pipelines in petrochemical and pollution control systems. The pipes offer tensile strengths of ≥790 MPa and yield strengths of ≥355 MPa, with excellent resistance to seawater (~0.01 mm/year corrosion rate) and reducing acids (~0.02 mm/year in 5% HCl). Their seamless design ensures zero leakage, critical for chemical processing and marine applications [Web ID: 11].
Seamless pipes are produced via cold drawing or extrusion, followed by annealing to optimize properties. Welded pipes are manufactured using ERW or EFW processes, with post-weld annealing optional due to the alloy’s low carbon content. Applications include flue gas desulfurization systems, sour gas wells, and chemical reactors, where Hastelloy C276 outperforms stainless steel 316 and Monel 400 in corrosive environments. The pipes are available with plain, beveled, or threaded ends, catering to diverse installation needs. Their higher cost compared to stainless steel is justified by reduced maintenance and longer service life in harsh conditions [Web ID: 6, 17].
Product Details: Hastelloy C276 Flanges
Hastelloy C276 flanges, conforming to ASTM B564 and ASME B16.5, are essential for connecting pipes in high-pressure and corrosive systems. Available in types such as weld neck, slip-on, socket weld, and blind, they range from 1/2 inch to 24 inches in nominal size, with pressure ratings from 150 to 2500. The flanges offer tensile strengths of ≥790 MPa and excellent corrosion resistance, with negligible pitting in seawater and reducing acids. Their forged construction ensures durability, making them ideal for offshore platforms, chemical plants, and power generation systems [Web ID: 21].
Flanges are produced via forging or machining from plates, with annealing at 1120-1180°C to enhance corrosion resistance. Welding, using matching filler metals (e.g., ERNiCrMo-4), ensures strong joints without compromising properties. Compared to Inconel 625 flanges, Hastelloy C276 offers superior resistance to reducing acids but lower high-temperature strength. Applications include pipeline terminations, valve connections, and heat exchanger assemblies, where the alloy’s reliability ensures leak-free performance. Surface treatments like pickling and polishing enhance corrosion resistance, particularly in pharmaceutical and marine environments [Web ID: 13, 21].
Comparison with Inconel Alloys and Other Materials
Property/Alloy | Hastelloy C276 | Inconel 625 | Monel 400 | 316 Stainless Steel |
---|---|---|---|---|
Nickel Content (%) | ~57 | ≥58 | ≥63 | 10–14 |
Tensile Strength (MPa) | ≥790 | ≥827 | 483–586 | ≥515 |
Yield Strength (MPa) | ≥355 | ≥414 | 172–310 | ≥205 |
Corrosion Resistance | Excellent (reducing/oxidizing) | Excellent (oxidizing) | Excellent (reducing) | Moderate (chloride SCC) |
Machinability | Moderate | Poor | Moderate | Good |
Weldability | Excellent | Excellent | Good | Good |
Max Temperature (°C) | 1040 | 1093 | 480 | 800 |
Hastelloy C276 outperforms Inconel 625 in reducing environments due to its higher molybdenum content, but Inconel 625 is superior in high-temperature oxidizing conditions. Monel 400 offers excellent corrosion resistance in reducing acids but lacks the strength and versatility of Hastelloy C276. Stainless steel 316 is more cost-effective but prone to chloride SCC, making it unsuitable for marine and chemical applications where Hastelloy C276 excels. The alloy’s balance of corrosion resistance, strength, and weldability makes it a top choice for critical piping systems [Web ID: 1, 15].
Applications and Industry Use
Hastelloy C276 pipes and flanges are widely used in industries requiring robust performance in corrosive and high-pressure environments. In chemical processing, they handle aggressive media like hydrochloric, sulfuric, and phosphoric acids in reactors and distillation columns. In marine engineering, the alloy’s resistance to seawater makes it ideal for heat exchangers, subsea pipelines, and offshore platform fittings. Petrochemical applications include sour gas wells and flue gas desulfurization systems, where Hastelloy C276’s resistance to pitting and SCC ensures reliability. The alloy is also used in pharmaceutical production for reactor vessels and piping systems, where its non-toxic nature and resistance to high-purity water are critical [Web ID: 6, 17].
Compared to Monel 400, Hastelloy C276 offers superior strength and corrosion resistance in oxidizing environments, while Inconel 625 is preferred for high-temperature applications like aerospace exhaust systems. Emerging applications include renewable energy systems, such as biofuel reactors and tidal energy converters, where the alloy’s durability reduces maintenance costs. Its compliance with NACE MR0175/ISO 15156 ensures suitability for oil and gas applications, while ASME Boiler and Pressure Vessel Code approval supports its use in nuclear and power generation systems [Web ID: 13, 20].
Recent Scientific Insights and Developments
Recent studies highlight Hastelloy C276’s evolving role in advanced piping systems. Research from 2024 demonstrates that optimized annealing processes reduce residual stresses in seamless pipes, improving fatigue resistance by 15%. Advances in surface treatments, such as plasma nitriding, have reduced corrosion rates in seawater by 20%, extending service life in marine applications. Laser welding techniques have enhanced the integrity of welded pipes, minimizing defects in high-pressure systems. Additive manufacturing research shows promise for producing complex Hastelloy C276 flanges, offering improved design flexibility for aerospace and chemical applications. The alloy’s resistance to biofouling in marine environments has also been noted, reducing maintenance in offshore systems [Web ID: 8, 24].
Conclusion
Hastelloy C276 (UNS N10276, W.Nr. 2.4819) is a versatile nickel-molybdenum-chromium alloy, offering unmatched corrosion resistance and mechanical strength for pipes and flanges in demanding environments. Its high molybdenum and tungsten content ensures superior performance in reducing and oxidizing media, while its low carbon content supports excellent weldability. Compared to Inconel 625, Monel 400, and stainless steel 316, Hastelloy C276 excels in chemical processing, marine, and petrochemical applications. Its seamless and welded pipes, along with forged flanges, provide reliable solutions for high-pressure and corrosive systems. Ongoing research continues to enhance its performance, solidifying Hastelloy C276’s role as a critical material in modern industrial applications.
You must be logged in to post a comment.