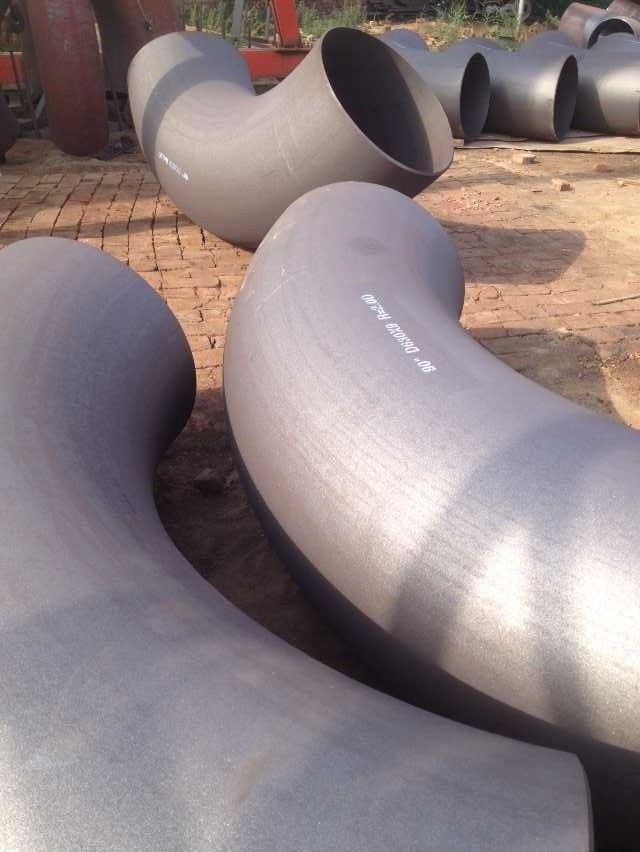
Steel Pipe Elbows Manufacturing Process: A Comprehensive Guide
Steel pipe elbows are essential components in piping systems, allowing for changes in direction within the pipeline. These fittings are widely used in industries such as oil and gas, petrochemicals, power plants, and construction, where robust and reliable connections are required to handle high pressure, temperature, and corrosive environments.
The manufacturing process of steel pipe elbows is highly specialized, involving various methods to ensure the final product meets stringent quality standards. This article provides a detailed overview of the steel pipe elbow manufacturing process, including the types of elbows, materials used, and the techniques employed to produce them.
Mandrel method Hot Forming Pipe Bending
Extrusion Method Pipe Bend
Hot Forming Method Pipe Bend
Hydraulic Bulge Method Pipe TEEs
What Are Steel Pipe Elbows?
A steel pipe elbow is a pipe fitting that allows for a directional change in a piping system. These elbows are typically available in various angles, such as 90 degrees, 45 degrees, and 180 degrees, to suit different piping layouts. They are classified based on their radius of curvature, material, and manufacturing method.
Types of Steel Pipe Elbows
Steel pipe elbows can be categorized into the following types based on their design and application:
- Short Radius (SR) Elbows:
- The radius of curvature is equal to the pipe diameter (1D).
- Used in tight spaces where compact layouts are required.
- Common in low-pressure systems.
- Long Radius (LR) Elbows:
- The radius of curvature is 1.5 times the pipe diameter (1.5D).
- Preferred in systems with high pressure and flow rates.
- Reduces friction and pressure loss.
- Reducing Elbows:
- Designed to connect pipes of different diameters.
- Used in systems where a gradual reduction in flow is required.
- Custom Elbows:
- Manufactured for specific applications with unique angles or dimensions.
Materials Used in Steel Pipe Elbows
Steel pipe elbows are made from various materials, depending on the application and operating conditions. Common materials include:
- Carbon Steel: Used in general-purpose applications with moderate pressure and temperature.
- Stainless Steel: Preferred for corrosive environments and high-temperature applications.
- Alloy Steel: Used in high-pressure and high-temperature systems, such as power plants and refineries.
- Duplex Stainless Steel: Offers excellent corrosion resistance and strength, suitable for offshore and chemical industries.
Steel Pipe Elbow Manufacturing Processes
The manufacturing of steel pipe elbows involves several specialized processes to ensure the product meets the required specifications for strength, durability, and dimensional accuracy. Below are the main methods used in the production of steel pipe elbows:
1. Mandrel Method (Hot Forming Process)
The mandrel method, also known as the hot forming process, is one of the most common techniques for manufacturing steel pipe elbows. This process involves heating a steel pipe and shaping it into an elbow using a mandrel and die.
Steps in the Mandrel Method:
- Cutting the Pipe:
- A straight steel pipe is cut to the required length, depending on the size of the elbow to be produced.
- Heating:
- The pipe is heated in a furnace to a high temperature (typically between 900°C and 1100°C) to make it malleable.
- Forming:
- The heated pipe is placed in a die and shaped into an elbow using a mandrel. The mandrel ensures the pipe retains its round cross-section during bending.
- Cooling:
- The formed elbow is cooled slowly to relieve internal stresses and maintain its structural integrity.
- Trimming and Beveling:
- Excess material is trimmed, and the ends of the elbow are beveled to prepare them for welding.
- Heat Treatment:
- The elbow undergoes heat treatment to improve its mechanical properties, such as strength and toughness.
- Inspection and Testing:
- The finished elbow is inspected for dimensional accuracy, surface defects, and mechanical properties. Non-destructive testing (NDT) methods, such as ultrasonic testing or radiographic testing, are often used.
2. Cold Forming Process
The cold forming process is used to manufacture smaller-diameter elbows and involves shaping the steel pipe at room temperature. This method is less common than the hot forming process but is suitable for applications where heat treatment is not required.
Steps in the Cold Forming Process:
- Cutting the Pipe:
- A straight steel pipe is cut to the required length.
- Forming:
- The pipe is placed in a hydraulic press or bending machine and shaped into an elbow using a die.
- Trimming and Beveling:
- The ends of the elbow are trimmed and beveled for welding.
- Inspection:
- The elbow is inspected for dimensional accuracy and surface quality.
3. Welded Elbow Manufacturing
In this method, steel plates or sheets are used to manufacture elbows. The plates are cut, rolled, and welded to form the desired shape. This process is typically used for large-diameter elbows.
Steps in Welded Elbow Manufacturing:
- Cutting the Steel Plate:
- A steel plate is cut into a specific shape based on the dimensions of the elbow.
- Rolling:
- The plate is rolled into a cylindrical shape using a rolling machine.
- Welding:
- The edges of the rolled plate are welded together to form a pipe.
- Shaping:
- The welded pipe is shaped into an elbow using a die or press.
- Heat Treatment:
- The elbow undergoes heat treatment to improve its mechanical properties.
- Inspection and Testing:
- The weld seam is inspected for defects using non-destructive testing methods.
4. Extrusion Method
The extrusion method is used to produce seamless elbows by extruding a solid billet into the desired shape. This process is suitable for high-pressure applications and produces elbows with excellent mechanical properties.
Steps in the Extrusion Method:
- Heating the Billet:
- A solid steel billet is heated to a high temperature.
- Piercing:
- The billet is pierced to create a hollow tube.
- Extrusion:
- The hollow tube is extruded through a die to form an elbow.
- Heat Treatment:
- The elbow undergoes heat treatment to enhance its strength and toughness.
- Inspection:
- The finished elbow is inspected for quality and dimensional accuracy.
5. Push Bending Method
The push bending method is a cost-effective process used for manufacturing elbows with a consistent wall thickness. This method involves pushing a steel pipe through a die to form the desired shape.
Steps in the Push Bending Method:
- Cutting the Pipe:
- A straight steel pipe is cut to the required length.
- Heating:
- The pipe is heated to make it malleable.
- Pushing:
- The heated pipe is pushed through a die to form the elbow.
- Cooling:
- The elbow is cooled slowly to relieve internal stresses.
- Inspection:
- The elbow is inspected for quality and dimensional accuracy.
Quality Control in Steel Pipe Elbow Manufacturing
To ensure the reliability and performance of steel pipe elbows, strict quality control measures are implemented throughout the manufacturing process. These measures include:
- Dimensional Inspection: Verifying the dimensions of the elbow, such as radius, angle, and wall thickness.
- Non-Destructive Testing (NDT): Using methods such as ultrasonic testing, radiographic testing, and magnetic particle testing to detect internal and surface defects.
- Mechanical Testing: Conducting tests to evaluate the elbow’s strength, toughness, and hardness.
- Hydrostatic Testing: Testing the elbow’s ability to withstand internal pressure without leaking or deforming.
Table: Comparison of Manufacturing Methods for Steel Pipe Elbows
Manufacturing Method | Key Features | Applications | Advantages | Disadvantages |
---|---|---|---|---|
Mandrel Method | Hot forming process using a mandrel and die | High-pressure and high-temperature systems | High strength, uniform structure | Requires heat treatment, higher cost |
Cold Forming | Shaping at room temperature | Small-diameter elbows | Cost-effective, no heat treatment needed | Limited to smaller sizes |
Welded Elbow | Made from steel plates or sheets | Large-diameter elbows | Suitable for large sizes, cost-effective | Weld seam may be a weak point |
Extrusion Method | Seamless elbows from solid billets | High-pressure applications | Seamless, excellent mechanical properties | Expensive, limited size range |
Push Bending | Pipe pushed through a die | General-purpose applications | Consistent wall thickness, cost-effective | Limited to standard sizes and angles |
Conclusion
The manufacturing process of steel pipe elbows is a highly specialized and precise operation that ensures these critical components meet the demands of various industries. Whether produced through the mandrel method, cold forming, welding, extrusion, or push bending, each method has its unique advantages and is suited to specific applications.
By understanding the different manufacturing processes and their characteristics, you can select the right type of steel pipe elbow for your project, ensuring optimal performance, durability, and cost-effectiveness.
You must be logged in to post a comment.