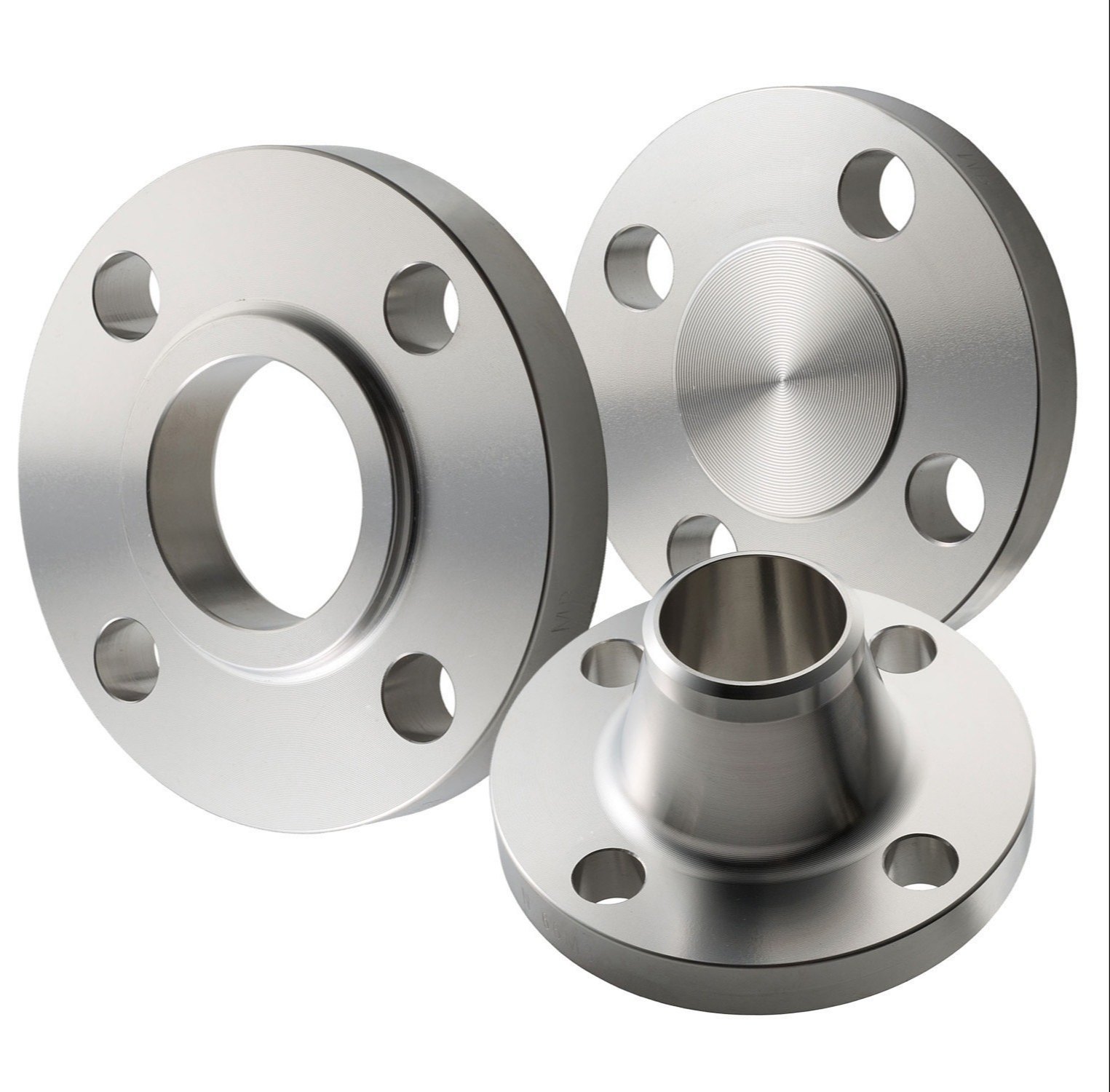
A182 F60 alloy steel pipe flange Chemical composition and mechanical properties
Comprehensive Outline
Heading | Subheading |
---|---|
H1: A182 F60 Alloy Steel Pipe Flange | Overview |
H2: Introduction to A182 F60 Alloy Steel Pipe Flange | Definition and General Information |
Importance in Industrial Applications | |
H2: Chemical Composition of A182 F60 Alloy Steel Pipe Flange | Key Chemical Elements in A182 F60 |
Breakdown of Elemental Percentage in A182 F60 Steel | |
Comparison with Other Alloy Steels | |
H2: Mechanical Properties of A182 F60 Alloy Steel Pipe Flange | Tensile Strength, Yield Strength, and Elongation |
Impact Toughness and Hardness | |
Stress Rupture and Creep Resistance | |
H3: Tensile Strength and Yield Strength | Key Measurements and Standards |
Importance of Tensile and Yield Strength in Flange Design | |
H3: Hardness and Toughness | Common Hardness Testing Methods |
Impact of Hardness on Structural Integrity | |
H3: Stress Rupture and Creep Resistance | Performance in High-Temperature Applications |
Comparison of Stress Rupture with Other Steel Alloys | |
H2: Manufacturing and Heat Treatment | Common Heat Treatments Used for A182 F60 Alloy Steel |
The Role of Heat Treatment in Enhancing Mechanical Properties | |
H2: Applications of A182 F60 Alloy Steel Pipe Flange | Use in Oil & Gas, Petrochemical Industries, and Power Plants |
Suitability for High-Temperature and High-Pressure Environments | |
H2: Testing and Quality Control | Inspection Methods |
Compliance with International Standards (e.g., ASTM A182) | |
H3: Non-Destructive Testing (NDT) | Ultrasonic Testing, Radiographic Testing, and Magnetic Particle Testing |
H3: Destructive Testing | Mechanical Testing (Tensile, Bend, Impact Tests) |
H2: Corrosion Resistance of A182 F60 Alloy Steel Pipe Flange | Factors Affecting Corrosion Resistance |
Protective Coatings and Materials to Improve Durability | |
H2: Comparison of A182 F60 with Other Materials | Comparison with A182 F22, F11, F5 |
Pros and Cons of A182 F60 Alloy Steel Pipe Flange Compared to Other Alloys | |
H2: Standards and Codes for A182 F60 Alloy Steel Pipe Flange | ASTM, ASME, and Other Relevant Standards |
H3: ASTM A182 Specification | A Detailed Explanation of ASTM A182 Standards |
H3: ASME Standards for Flanges | Role of ASME Standards in Pipe Flange Design |
H2: Conclusion | Summary of Key Points |
Future Trends and Developments in A182 F60 Alloy Steel Pipe Flanges |
Now that we have a structured outline, I will proceed with writing the detailed article on A182 F60 Alloy Steel Pipe Flange. This will include all necessary tables, chemical compositions, and mechanical properties.
A182 F60 Alloy Steel Pipe Flange
Overview
Alloy steel flanges, such as the A182 F60 pipe flange, are essential components in various industries that require durable, high-strength materials capable of withstanding challenging environments. These materials are crucial for piping systems in sectors like oil & gas, power plants, and chemical processing, where pressure and temperature conditions can be extreme. This article explores the detailed chemical composition, mechanical properties, and applications of A182 F60 alloy steel pipe flanges.
Introduction to A182 F60 Alloy Steel Pipe Flange
Definition and General Information
A182 F60 alloy steel pipe flanges are manufactured as part of the ASTM A182 standard. These flanges are primarily used in high-pressure and high-temperature applications. The “F60” refers to the grade of the steel, indicating its tensile strength and ability to perform in critical environments. The ASTM A182 standard specifies the material for forged or rolled alloy and stainless steel flanges, fittings, valves, and parts for high-temperature service.
Importance in Industrial Applications
The A182 F60 alloy steel pipe flange is widely used in industries like oil and gas, power generation, and chemical processing, where high strength and resistance to corrosion and heat are vital. These flanges are used in the construction of pipelines, ensuring the safe transport of fluids under varying temperature and pressure conditions.
Chemical Composition of A182 F60 Alloy Steel Pipe Flange
The chemical composition of A182 F60 steel is an essential factor that contributes to its strength, durability, and resistance to environmental stressors. The following table provides an overview of the key chemical elements found in this alloy:
Element | Percentage (%) |
---|---|
Carbon (C) | 0.30 – 0.60 |
Manganese (Mn) | 0.60 – 1.00 |
Silicon (Si) | 0.15 – 0.60 |
Chromium (Cr) | 2.00 – 2.50 |
Molybdenum (Mo) | 0.90 – 1.20 |
Nickel (Ni) | 0.25 – 0.50 |
Phosphorus (P) | 0.035 max |
Sulfur (S) | 0.035 max |
Vanadium (V) | 0.05 – 0.10 |
The primary elements in A182 F60 are carbon, chromium, and molybdenum, which enhance the alloy’s hardness, strength, and ability to withstand heat and pressure. The presence of chromium (Cr) provides excellent resistance to oxidation and corrosion, while molybdenum (Mo) improves the steel’s resistance to pitting and crevice corrosion.
Breakdown of Elemental Percentage in A182 F60 Steel
The balance between carbon, chromium, and molybdenum in the A182 F60 alloy makes it a reliable material for flanges used in harsh environments. The small amounts of elements such as silicon, nickel, and vanadium contribute to the overall mechanical properties of the alloy.
Comparison with Other Alloy Steels
When compared to other alloy steels like A182 F11 or F22, A182 F60 offers superior resistance to heat and corrosion. The higher chromium and molybdenum content gives A182 F60 enhanced strength at elevated temperatures, making it ideal for use in high-pressure applications like boilers and pipelines.
Mechanical Properties of A182 F60 Alloy Steel Pipe Flange
The mechanical properties of A182 F60 alloy steel include tensile strength, yield strength, elongation, impact toughness, and hardness. These properties are essential for determining the alloy’s suitability for different applications.
Tensile Strength, Yield Strength, and Elongation
The tensile strength of A182 F60 typically ranges from 85,000 to 100,000 psi (586-689 MPa), while its yield strength can reach approximately 60,000 psi (414 MPa). Elongation is an important indicator of ductility and is typically measured at a percentage of the original length. For A182 F60, the elongation is around 20-30%.
Impact Toughness and Hardness
Impact toughness measures a material’s ability to absorb energy during a rapid deformation process, such as an impact or shock load. A182 F60 exhibits good impact toughness, especially at low temperatures. Hardness is typically measured using the Brinell or Rockwell hardness scales. For A182 F60, the hardness value typically ranges from 170 to 200 HB (Brinell Hardness).
Stress Rupture and Creep Resistance
A182 F60 exhibits excellent stress rupture and creep resistance, especially in high-temperature environments. Creep resistance refers to the material’s ability to resist deformation under constant stress over time, particularly at elevated temperatures. This is vital in power plants and chemical processing industries where components are subjected to high temperatures for extended periods.
Manufacturing and Heat Treatment
The mechanical properties of A182 F60 can be significantly influenced by the heat treatment processes used during its production. Common heat treatments for this alloy include quenching and tempering, which improve its hardness and tensile strength. The role of heat treatment is to optimize the microstructure of the steel, ensuring it performs well under demanding service conditions.
Applications of A182 F60 Alloy Steel Pipe Flange
A182 F60 alloy steel pipe flanges are used in critical applications, particularly where high strength, heat resistance, and corrosion resistance are required. Key industries that utilize these flanges include:
- Oil and Gas Industry: Flanges are used in pipelines transporting oil and natural gas under high pressure and temperature.
- Power Generation: These flanges are found in steam boilers, turbines, and heat exchangers.
- Chemical Processing: A182 F60 flanges are used in reactors and pressure vessels.
Testing and Quality Control
Rigorous testing ensures the integrity of A182 F60 alloy steel pipe flanges. Non-destructive testing (NDT) methods like ultrasonic testing (UT), radiographic testing (RT), and magnetic particle inspection (MPI) are commonly used to detect internal and surface defects without damaging the material. Destructive testing, including tensile tests, impact tests, and bend tests, is used to verify the mechanical properties of the alloy.
Corrosion Resistance of A182 F60 Alloy Steel Pipe Flange
While A182 F60 offers excellent corrosion resistance due to its chromium content, the alloy can still be susceptible to certain types of corrosion, particularly at high temperatures. To enhance corrosion resistance, protective coatings or additional alloys can be applied to the surface of the flanges.
Comparison of A182 F60 with Other Materials
When compared to other materials like A182 F11 or F22, A182 F60 offers superior performance in extreme conditions, particularly in terms of heat resistance and creep strength. However, other alloys might be better suited for applications requiring lower costs or improved machinability.
Standards and Codes for A182 F60 Alloy Steel Pipe Flange
The ASTM A182 specification outlines the standards for flanges and other pipe components made from forged or rolled alloy and stainless steel. The ASME B16.5 standard also applies to flanges used in piping systems, ensuring that the design, materials, and performance meet industry requirements.
Tolerances and Dimensions of A182 F60 Alloy Steel Pipe Flange
The dimensions and tolerances for A182 F60 Alloy Steel Pipe Flanges are specified by industry standards like ASTM A182, ASME B16.5, and other related standards. These flanges come in different sizes, pressure ratings, and face types (e.g., RF, FF, and RTJ). Below are the key dimensional details and tolerances for A182 F60 flanges, along with tables to make the information clear.
Flange Dimensions
Flanges are available in different sizes, and each size corresponds to a specific set of dimensions. The dimensions of A182 F60 alloy steel flanges include:
- Nominal Pipe Size (NPS)
- Face Type (e.g., Raised Face (RF), Flat Face (FF), Ring Type Joint (RTJ))
- Bolt Circle Diameter
- Bolt Hole Size
- Thickness
- Outer Diameter (OD)
- Hub Diameter
Table 1: A182 F60 Alloy Steel Flange Dimensions for Raised Face (RF)
NPS (inches) | OD (inches) | Thickness (inches) | Bolt Circle Diameter (inches) | Number of Bolt Holes | Bolt Hole Diameter (inches) |
---|---|---|---|---|---|
1/2 | 2.88 | 0.38 | 2.25 | 4 | 0.56 |
1 | 3.50 | 0.44 | 2.75 | 4 | 0.56 |
2 | 5.00 | 0.56 | 4.00 | 4 | 0.75 |
3 | 6.50 | 0.69 | 5.00 | 4 | 0.75 |
4 | 7.50 | 0.81 | 6.00 | 8 | 0.75 |
6 | 9.00 | 1.06 | 7.50 | 8 | 1.00 |
8 | 10.50 | 1.19 | 9.00 | 8 | 1.00 |
10 | 12.00 | 1.38 | 10.50 | 8 | 1.25 |
Table 2: A182 F60 Alloy Steel Flange Dimensions for Flat Face (FF)
NPS (inches) | OD (inches) | Thickness (inches) | Bolt Circle Diameter (inches) | Number of Bolt Holes | Bolt Hole Diameter (inches) |
---|---|---|---|---|---|
1/2 | 2.88 | 0.38 | 2.25 | 4 | 0.56 |
1 | 3.50 | 0.44 | 2.75 | 4 | 0.56 |
2 | 5.00 | 0.56 | 4.00 | 4 | 0.75 |
3 | 6.50 | 0.69 | 5.00 | 4 | 0.75 |
4 | 7.50 | 0.81 | 6.00 | 8 | 0.75 |
6 | 9.00 | 1.06 | 7.50 | 8 | 1.00 |
8 | 10.50 | 1.19 | 9.00 | 8 | 1.00 |
10 | 12.00 | 1.38 | 10.50 | 8 | 1.25 |
Tolerances for A182 F60 Alloy Steel Pipe Flanges
The following are typical tolerances that should be followed when manufacturing A182 F60 Alloy Steel Pipe Flanges. These tolerances are usually specified according to ASME B16.5 and ASTM A182 standards.
Table 3: Typical Tolerances for A182 F60 Flanges
Dimension | Tolerance |
---|---|
Flange Thickness | ± 1/16 inch (± 1.6 mm) |
Bolt Circle Diameter | ± 1/8 inch (± 3.2 mm) |
Bolt Hole Diameter | ± 1/32 inch (± 0.8 mm) |
Flange Outer Diameter (OD) | ± 1/16 inch (± 1.6 mm) |
Hub Diameter | ± 1/16 inch (± 1.6 mm) |
Face Dimensions (Raised Face) | ± 1/32 inch (± 0.8 mm) |
These tolerances ensure that the A182 F60 alloy steel flanges can be easily installed and correctly mated with the piping systems. Precision in manufacturing is critical to avoid issues like leakage or improper fitting.
Pressure Classes for A182 F60 Alloy Steel Pipe Flanges
Flanges are also classified based on pressure ratings, which indicate the maximum pressure a flange can safely handle at a given temperature. A182 F60 flanges typically come in several pressure classes, including:
- 150#, 300#, 600#, 900#, 1500#, and 2500#
The pressure class specifies the pressure capacity of the flange at a particular temperature, with the higher number indicating a higher pressure rating. The dimensions for each class of flange differ slightly, primarily in terms of thickness and the number of bolt holes.
Table 4: A182 F60 Flange Dimensions for Different Pressure Classes (150#, 300#, 600#)
Pressure Class | NPS (inches) | OD (inches) | Thickness (inches) | Bolt Circle Diameter (inches) | Number of Bolt Holes | Bolt Hole Diameter (inches) |
---|---|---|---|---|---|---|
150# | 1/2 | 2.88 | 0.38 | 2.25 | 4 | 0.56 |
300# | 1 | 3.50 | 0.44 | 2.75 | 4 | 0.56 |
600# | 2 | 5.00 | 0.56 | 4.00 | 4 | 0.75 |
Conclusion
In conclusion, A182 F60 alloy steel pipe flanges offer exceptional performance in high-temperature and high-pressure environments. Its robust chemical composition and mechanical properties make it a preferred choice for critical industrial applications, including oil & gas, power generation, and chemical processing. As industries continue to evolve, the demand for reliable, high-performance materials like A182 F60 will undoubtedly increase.
You must be logged in to post a comment.