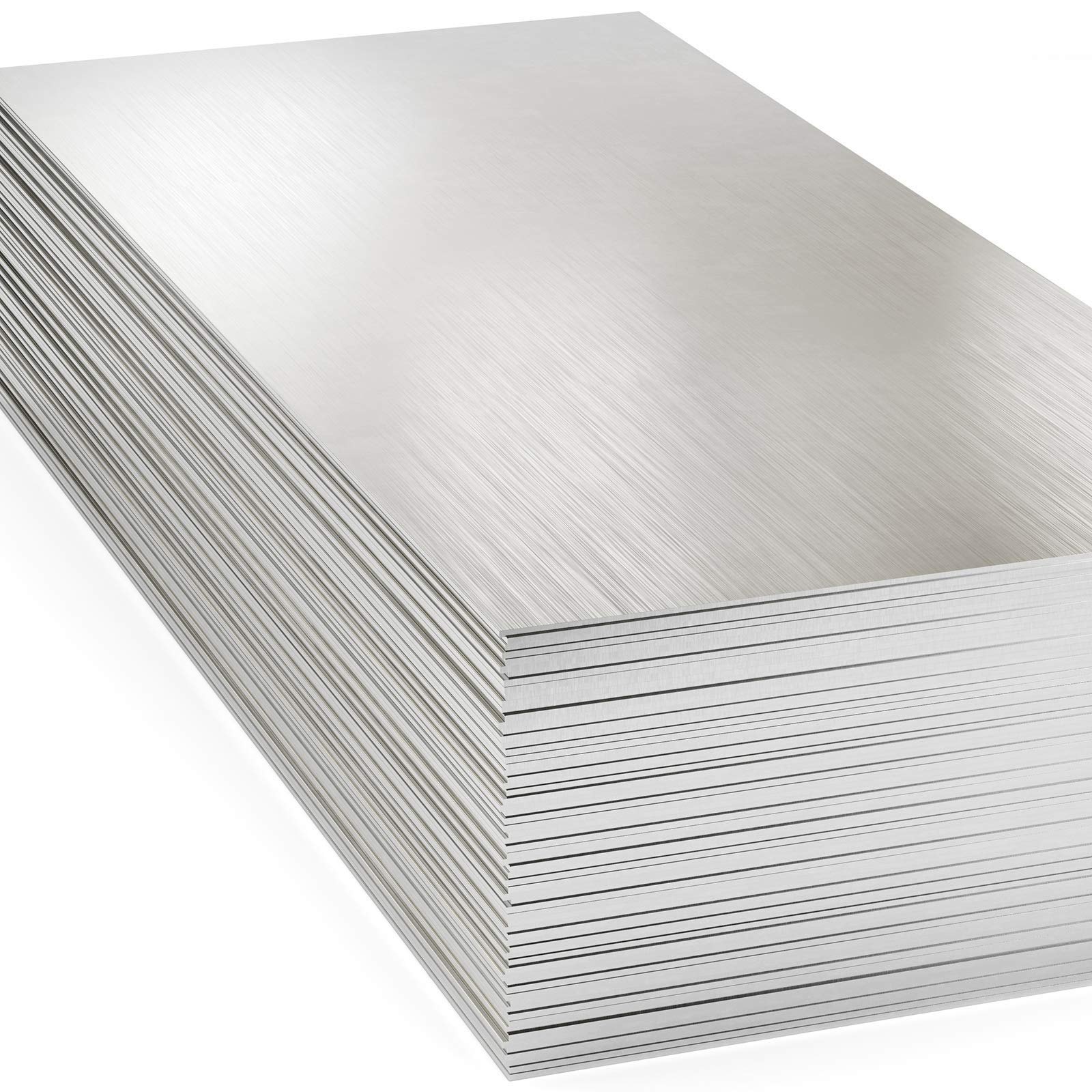
Incoloy Superalloy Alloy A286 | Sheet | Plate | Pipe Fitting: Comprehensive Analysis
Incoloy Alloy A286, also known by its UNS designation S66286, is a high-performance iron-nickel-chromium-based superalloy widely used in high-temperature and high-stress industrial applications. Its combination of strength, corrosion resistance, and oxidation resistance at elevated temperatures makes it a preferred choice for manufacturing sheets, plates, and pipe fittings.
This article delves into the properties, applications, advantages, and considerations of A286 sheets, plates, and pipe fittings, providing an in-depth guide for professionals across industries.
1. Introduction to Incoloy Alloy A286
Incoloy A286 is a precipitation-hardenable superalloy renowned for its excellent mechanical properties and resistance to oxidation in high-temperature environments. Developed for extreme operational conditions, it is primarily used in applications requiring durability, strength, and resistance to thermal degradation.
Key Characteristics:
- UNS Designation: S66286
- Common Forms: Sheet, plate, pipe fittings, fasteners, and flanges.
- Applications: Aerospace, gas turbines, oil and gas pipelines, and chemical processing plants.
- Temperature Resistance: Retains mechanical properties up to 1300°F (704°C).
2. Properties of Incoloy A286 Superalloy
The superior performance of A286 in extreme environments is attributed to its unique properties:
Mechanical Properties
Property | Value |
---|---|
Tensile Strength (Annealed) | 930 MPa (min) |
Yield Strength | 590 MPa (min) |
Elongation | 15–20% |
Hardness | Rockwell C30–C40 |
Corrosion Resistance
- High resistance to oxidation in temperatures up to 1300°F.
- Excellent performance in environments containing chlorides, acids, and alkaline compounds.
Oxidation Resistance
- Operates efficiently in high-temperature environments without forming damaging oxide layers.
2. Mechanical Properties: Comparative Strength and Ductility
Incoloy A-286 exhibits superior mechanical performance under high-temperature conditions:
- Tensile Strength: The alloy maintains structural integrity up to 1300°F (704°C), comparable to Inconel 718.
- Ductility in Notched Sections: A-286 surpasses many other high-temperature alloys in notched rupture strength, making it highly reliable under stress concentrations.
- Modulus of Elasticity (E): The stiffness decreases with temperature, as expected in high-temperature applications:
- 70°F: 28.8 x 10³ ksi
- 1000°F: 23.7 x 10³ ksi
- 1500°F: 18.7 x 10³ ksi
Comparative Analysis:
- A-286 vs. Inconel 718: While both alloys excel in high-temperature applications, Inconel 718 offers higher tensile strength at temperatures above 1300°F. However, A-286’s better ductility at lower temperatures makes it preferable for turbine wheels and blades.
- A-286 vs. Type 310 Stainless Steel: Type 310 stainless lacks the precipitation-hardening capabilities and high tensile strength of A-286.
3. Chemical Composition of Alloy A286
The chemical composition of Incoloy A286 is meticulously designed to enhance its strength, corrosion resistance, and temperature tolerance.
Element | Percentage |
---|---|
Iron (Fe) | Balance |
Nickel (Ni) | 24–27% |
Chromium (Cr) | 13.5–16% |
Molybdenum | 1–1.5% |
Titanium | 1.9–2.35% |
Aluminum | 0.15–0.5% |
Carbon | 0.08% (max) |
Vanadium | 0.1–0.5% |
Each element plays a critical role:
- Nickel: Provides toughness and resistance to corrosion.
- Chromium: Improves oxidation resistance.
- Titanium & Aluminum: Enhance precipitation hardening.
Comparative Note: When compared to alloys like Inconel 718 (also nickel-based), Incoloy A-286 has lower molybdenum content but higher titanium levels, focusing more on ductility and aging-induced strength rather than extreme corrosion resistance.
3. Thermal Properties
- Melting Range: 2500–2600°F, placing it among the higher-performing superalloys.
- Thermal Expansion: The coefficient increases with temperature:
- 200°F: 9.17 × 10⁻⁶ in/in/°F
- 1300°F: 9.94 × 10⁻⁶ in/in/°F
- 1400°F: 10.3 × 10⁻⁶ in/in/°F
- Thermal Conductivity: The alloy offers moderate conductivity for a high-temperature alloy:
- 302°F: 104.2 BTU-in/hr/ft²/°F
- 1112°F: 165.0 BTU-in/hr/ft²/°F
Comparative Insight:
- A-286 vs. Hastelloy X: Hastelloy X exhibits higher thermal stability above 1400°F, making it more suitable for extreme conditions, but A-286 offers better machinability and cost advantages.
4. Corrosion Resistance
Incoloy A-286 performs excellently under specific corrosive environments:
- At 1300°F: Corrosion resistance is excellent in jet engine environments.
- At 1500°F: Oxidation resistance is comparable to Type 310 stainless steel.
- Specific Media Ratings:
- Nitric Acid: Good
- Sulfuric Acid: Moderate
- Sea Water: Moderate
- Humidity: Excellent
Comparative Evaluation:
- A-286 vs. Inconel 718: Inconel 718, with its higher molybdenum and niobium content, shows better pitting and crevice corrosion resistance in chloride environments.
- A-286 vs. Type 316 Stainless: Type 316 shows better general corrosion resistance but lacks A-286’s high-temperature oxidation resistance.
5. Heat Treatment and Hardening
Heat treatment is key to achieving A-286’s desired mechanical properties:
- Solution Treatment:
- 1800°F for 1 hour (for rupture strength) or 1650°F for 2 hours (for better ductility and hardness).
- Aging:
- 1300–1400°F for 12–16 hours; air cooling produces ~300 BHN hardness.
- An optional two-cycle treatment enhances notch rupture strength and hardness.
Comparative Aspect:
- A-286’s precipitation hardening capability allows for greater strength consistency and repeatability, a feature less prominent in alloys like Type 310 stainless or Hastelloy X.
6. Workability: Machinability and Weldability
- Cold Working: A-286 can be cold drawn or formed in the solution-treated condition. It work-hardens rapidly.
- Machinability: Easier to machine than nickel-based grades like Inconel 718 but stiffer than Types 316 and 310 stainless steels.
- Weldability: Fusion welding is challenging due to heat-affected zone (HAZ) cracking risks. JBK-75 alloy is recommended if welding is necessary.
Industry Implications:
- A-286 vs. Inconel 718: A-286 is easier to machine but less weldable, making it more suitable for fasteners and turbine blades.
- A-286 vs. Hastelloy X: Hastelloy X is more weldable, especially for large structural components.
7. Applications
Incoloy A-286 is favored for high-temperature applications requiring a balance of strength, ductility, and corrosion resistance:
- Aerospace: Jet engines, turbine wheels and blades, afterburner parts.
- Automotive: High-temperature fasteners.
- Industrial: Superchargers, high-temperature casings, and frames.
Comparative Note:
- A-286 vs. Inconel 625: While Inconel 625 is more corrosion-resistant in seawater environments, A-286 excels in high-temperature, oxidizing conditions.
- A-286 vs. Type 310 Stainless: Type 310 finds applications in less mechanically demanding high-temperature environments.
8. Summary of Comparative Strengths and Weaknesses
Aspect | Incoloy A-286 | Inconel 718 | Hastelloy X | Type 310 Stainless |
---|---|---|---|---|
High-Temp Strength | Excellent (up to 1300°F) | Superior (>1300°F) | Moderate | Moderate |
Corrosion Resistance | Excellent (oxidizing) | Excellent (general & pitting) | Excellent (oxidizing) | Good |
Workability (Machining) | Moderate | Difficult | Moderate | Easy |
Weldability | Difficult | Moderate | Good | Good |
Cost-Effectiveness | Moderate | High | High | Low |
4. Manufacturing Forms of Incoloy A286
Incoloy A286 is available in multiple manufacturing forms, tailored to specific industrial needs. The three most common forms are:
1. Sheet
- Thin, flat pieces used in high-temperature environments.
- Commonly found in aerospace applications like jet engine components.
2. Plate
- Thicker than sheets and ideal for structural applications.
- Used in power generation equipment, heat exchangers, and gas turbines.
3. Pipe Fittings
- Includes elbows, tees, reducers, and couplings.
- Designed for use in high-pressure piping systems.
5. Applications of A286 Sheets
A286 sheets are lightweight yet strong, making them ideal for:
- Aerospace Components: Used in jet engine combustion chambers, ducting, and exhausts.
- Heat Exchangers: Operate efficiently in high-temperature environments.
- Industrial Gaskets: Provide excellent sealing in harsh conditions.
6. Applications of A286 Plates
The high strength and resistance to wear make A286 plates suitable for:
- Power Generation Plants: Structural components in steam and gas turbines.
- Chemical Industry: Equipment subjected to corrosive substances.
- Nuclear Reactors: Withstand radiation and high heat.
7. Applications of A286 Pipe Fittings
Pipe fittings made from A286 are essential in:
- Oil & Gas Pipelines: Withstand high pressures and corrosive environments.
- Chemical Processing Plants: Transport of aggressive chemicals.
- High-Temperature Piping Systems: Used in furnaces and boilers.
8. Heat Treatment of A286 Superalloy
Heat Treatment Process:
- Solution Annealing: Heating to 1800°F (982°C) followed by rapid cooling to dissolve precipitates.
- Aging/Precipitation Hardening: Heating to 1325°F (718°C) to allow the formation of secondary precipitates for added strength.
Heat treatment enhances:
- Tensile Strength
- Creep Resistance
- Stress Rupture Properties
9. Advantages of A286 Sheets, Plates, and Pipe Fittings
- High Strength: Exceptional durability under extreme stresses.
- Corrosion Resistance: Superior resistance to pitting, oxidation, and chloride attacks.
- Temperature Stability: Retains properties up to 1300°F.
- Longevity: Prolonged service life in challenging environments.
10. Comparative Analysis: A286 vs Other Alloys
A286 vs Inconel 718
Property | A286 | Inconel 718 |
---|---|---|
Max Temperature | 1300°F | 1400°F |
Cost | Moderate | High |
Corrosion Resistance | Excellent | Superior |
A286 vs 304/316 Stainless Steel
Property | A286 | 304/316 Stainless |
---|---|---|
Strength | Higher | Moderate |
High-Temperature Use | Up to 1300°F | Up to 1000°F |
Corrosion Resistance | Superior | Good |
11. Specifications and Standards for A286 Products
ASTM and ASME Standards
- ASTM A453: Governs the mechanical properties of A286.
- ASME B16.9: Specifies dimensions for pipe fittings.
12. Factors to Consider When Choosing A286 Products
- Temperature Range: Ensure suitability for your operational temperature.
- Pressure Requirements: Check compatibility with system pressures.
- Chemical Exposure: Assess corrosion resistance in your environment.
13. Maintenance of A286 Sheets, Plates, and Pipe Fittings
Best Practices:
- Regular inspection for wear and corrosion.
- Clean with non-abrasive materials.
- Apply protective coatings for extended longevity.
14. Challenges in Working with A286 Alloy
- Machining Difficulty: Requires carbide tools and advanced techniques.
- High Cost: Material and processing are more expensive than standard steels.
15. Frequently Asked Questions (FAQs)
1. What makes A286 unique?
Its ability to retain mechanical strength and corrosion resistance at high temperatures up to 1300°F.
2. Where is A286 commonly used?
In aerospace, power generation, oil & gas pipelines, and chemical industries.
3. How does A286 compare to Inconel?
Inconel offers higher temperature resistance, but A286 is more cost-effective for moderate high-temperature applications.
4. Can A286 be welded?
Yes, A286 can be welded using TIG, MIG, or other standard welding techniques.
Incoloy A-286 alloy represents a well-balanced material for high-temperature applications where strength, corrosion resistance, and workability must coexist. Its ease of machining, excellent oxidation resistance, and tailored heat treatment processes make it versatile for demanding environments. However, in applications requiring extreme corrosion resistance or welding, alternative alloys like Inconel 718 or Hastelloy X may be more suitable.
You must be logged in to post a comment.