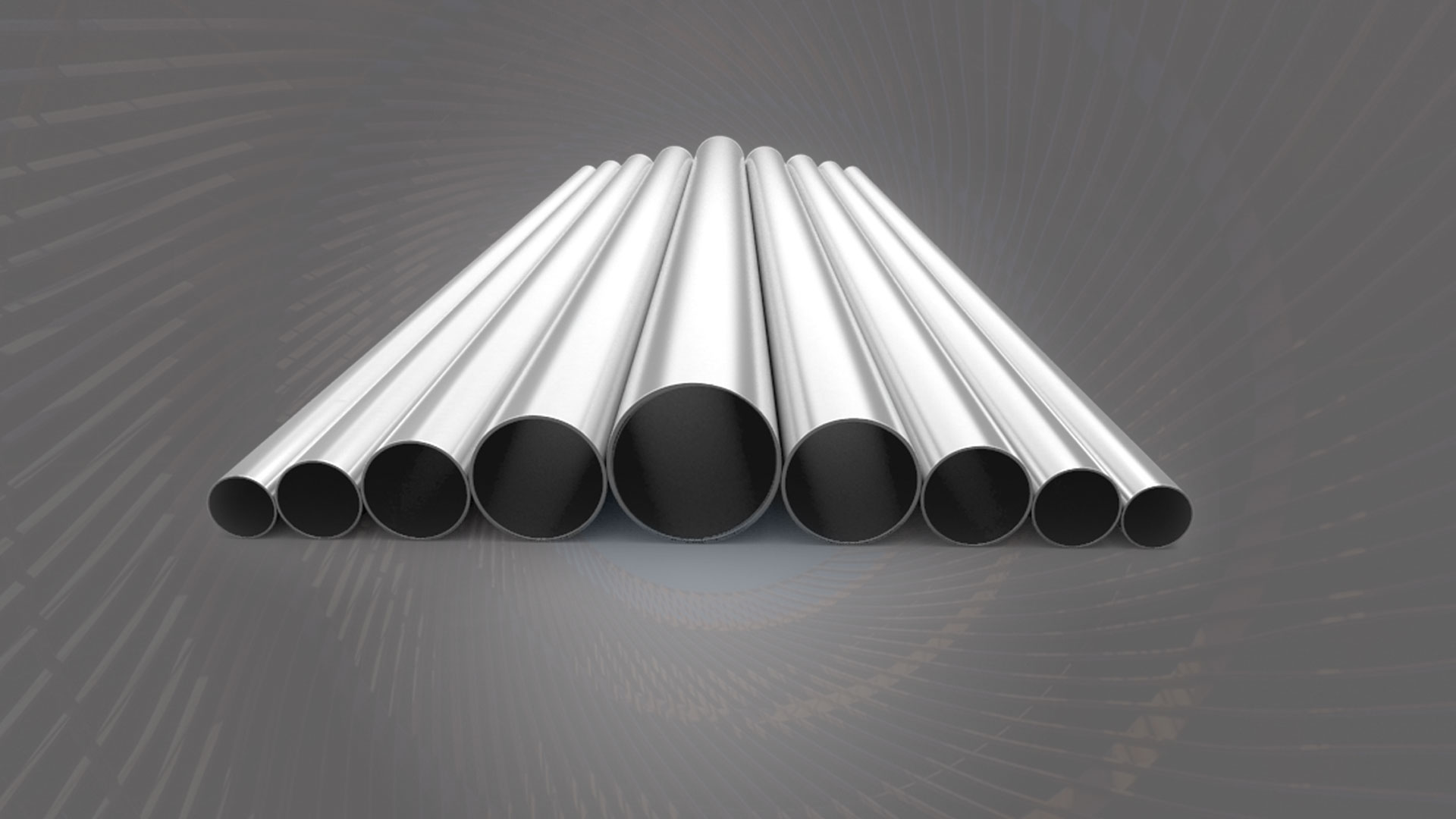
Comprehensive Guide on the Manufacturing Process of Nickel Alloy Seamless Pipe & Tube
Outline
Main Topics | Subtopics |
---|---|
Introduction to Nickel Alloy Pipes & Tubes | – What are Nickel Alloy Seamless Pipes & Tubes? – Properties of Nickel Alloys – Applications |
Nickel Alloy Grades & Standards | – Overview of ASTM Standards – Common Nickel Alloy Grades – Comparison of Key Specifications |
Material Selection | – Properties of Nickel Alloys – Selection Criteria for Different Applications – Material Challenges |
Manufacturing Process Overview | – Definition of Seamless Pipe Production – Advantages Over Welded Pipes – Key Stages in Manufacturing |
Step 1: Raw Material Preparation | – Nickel Alloy Procurement – Quality Assurance of Raw Materials – Billet Selection Process |
Step 2: Hot Extrusion Process | – Heating Process – Extrusion Techniques – Managing Pipe Wall Thickness and Diameter |
Step 3: Piercing and Rolling | – Rotary Piercing Process – Pilgering Technique – Tube Sizing and Shaping |
Step 4: Heat Treatment | – Importance of Heat Treatment – Annealing Process for Nickel Alloys – Stress-Relieving Procedures |
Step 5: Cold Drawing | – Achieving Precise Dimensions – Improvement in Surface Finish – Enhancing Mechanical Properties |
Step 6: Straightening and Sizing | – Final Dimension Adjustments – Advanced Straightening Techniques – Sizing Tolerances |
Step 7: Surface Treatment | – Polishing and Cleaning – Surface Testing for Defects – Protective Coatings |
Step 8: Non-Destructive Testing (NDT) | – Ultrasonic Testing – Eddy Current Testing – Visual and Dimensional Inspections |
Technical Specifications and Size Range | – Standard Dimensions (Φ3 – Φ600mm, 0.5 – 30mm thickness) – Length ≤ 12000mm – Customization Capabilities |
Comparison Between Nickel Alloy Seamless and Welded Pipes | – Differences in Strength and Reliability – Cost and Manufacturing Time Comparison |
Applications of Nickel Alloy Seamless Pipes & Tubes | – Use in Petrochemical Industry – Applications in Aerospace – Marine and Energy Applications |
Challenges in Manufacturing | – Handling Material Strength at High Temperatures – Avoiding Defects During Extrusion and Rolling |
Future Trends in Nickel Alloy Pipe Production | – Innovations in Manufacturing Techniques – Development of New Nickel Alloys – Focus on Sustainability |
FAQs on Nickel Alloy Seamless Pipes | – Common Queries Answered – Guidance for Selection and Maintenance |
Introduction to Nickel Alloy Seamless Pipe & Tube
Nickel alloy seamless pipes and tubes play an essential role in various industrial applications requiring materials with exceptional corrosion resistance, heat resistance, and mechanical strength. These products are especially suited for demanding environments, including chemical processing, aerospace, power generation, and marine industries.
Nickel alloys, primarily composed of nickel along with other elements like chromium, molybdenum, and iron, exhibit outstanding properties such as high-temperature stability, resistance to oxidation, and compatibility with corrosive environments. This makes them indispensable for heat exchangers, condensers, and pressure vessels.
The seamless nature of these pipes eliminates any risk of welding-related weaknesses, making them highly durable and preferred for high-pressure and high-temperature systems.
Nickel Alloy Grades & Standards
Nickel alloy seamless pipes and tubes must comply with stringent standards to ensure quality, reliability, and safety in critical applications. These standards specify chemical composition, mechanical properties, and testing requirements.
Key ASTM Standards
- ASTM B161: Covers seamless nickel (UNS N02200) pipes.
- ASTM B167: Focuses on nickel-chromium alloy seamless pipes.
- ASTM B444: Specifies nickel-chromium-molybdenum alloy pipes for corrosion resistance.
- ASTM B622: Governs seamless pipe production for nickel-molybdenum alloys.
Common Nickel Alloy Grades
- Nickel 200/201: High corrosion resistance in reducing environments.
- Inconel® 600/625: Superior strength and oxidation resistance.
- Monel® 400/K500: Resistance to marine and acidic environments.
- Hastelloy® C276/C22: Excellent performance against highly corrosive media.
Technical Specifications and Size Range
Standard Dimensions
- Outside Diameter: Φ3mm to Φ600mm
- Wall Thickness: 0.5mm to 30mm
- Length: Up to 12000mm
- Customization: Available upon request.
Specifications Table
Diameter (mm) | Wall Thickness (mm) | Length (mm) |
---|---|---|
3 – 25 | 0.5 – 2.5 | 1000 – 6000 |
26 – 100 | 1.0 – 10.0 | 2000 – 9000 |
101 – 300 | 2.0 – 20.0 | 3000 – 12000 |
301 – 600 | 5.0 – 30.0 | Custom Sizes |
Popular Nickel Alloy Seamless Pipes and Tubes Grades
The following table showcases the popular grades of nickel alloy seamless pipes and tubes, including trade names, UNS numbers, and corresponding ASTM specifications.
Nickel Alloys | Trade Name* | UNS # | Specifications |
---|---|---|---|
Nickel 200 | – | N02200 | ASTM B161, ASTM B725 |
Nickel 201 | – | N02201 | ASTM B161, ASTM B725 |
Inconel 600 | Inconel® 600 | N06600 | ASTM B167, ASTM B517 |
Inconel 625 | Inconel® 625 | N06625 | ASTM B444, ASTM B704, ASTM B705 |
Incoloy 800 | Incoloy® 800 | N08800 | ASTM B407, ASTM B514, ASTM B515 |
Incoloy 825 | Incoloy® 825 | N08825 | ASTM B423, ASTM B704, ASTM B705 |
Monel 400 | Monel® 400 | N04400 | ASTM B165, ASTM B725 |
Monel K500 | Monel® K500 | N05500 | ASTM B865 |
Hastelloy C276 | Hastelloy® C276 | N10276 | ASTM B622, ASTM B619, ASTM B626, ASTM B575 |
Hastelloy C22 | Hastelloy® C22 | N06022 | ASTM B622, ASTM B619, ASTM B626, ASTM B575 |
Alloy 20 | Carpenter® 20 | N08020 | ASTM B729 |
Nickel Alloy Seamless Pipes and Tubes: Size Range
Nickel alloy seamless pipes and tubes are available in various sizes to suit diverse industrial needs. Below is a detailed table outlining product dimensions, including outer diameter (OD), wall thickness (WT), and length in both imperial and metric units.
Products | OD | WT | Length |
---|---|---|---|
Inch | MM | Inch | |
Nickel Alloy Pipes (Small Sizes) | 0.125 – 1.0 | 3 – 25 | 0.02 – 0.1 |
Nickel Alloy Pipes (Medium Sizes) | 1.0 – 4.0 | 26 – 100 | 0.04 – 0.4 |
Nickel Alloy Pipes (Large Sizes) | 4.0 – 24.0 | 101 – 600 | 0.08 – 1.2 |
Customized Sizes | As required | As required | As required |
Nickel Alloy Seamless Pipes and Tubes: Chemical Composition
The chemical composition of nickel alloy seamless pipes and tubes determines their properties, such as corrosion resistance, strength, and suitability for high-temperature environments. Below is the typical composition for key nickel alloy grades:
Alloy | Nickel (Ni) | Chromium (Cr) | Iron (Fe) | Molybdenum (Mo) | Copper (Cu) | Others |
---|---|---|---|---|---|---|
Nickel 200 | ≥ 99.0% | – | ≤ 0.40% | – | – | Carbon (C): ≤ 0.15% |
Inconel 600 | 72.0% min. | 14.0 – 17.0% | 6.0 – 10.0% | – | – | Carbon (C): ≤ 0.15%, Mn: ≤ 1.0% |
Inconel 625 | 58.0% min. | 20.0 – 23.0% | ≤ 5.0% | 8.0 – 10.0% | – | Nb: 3.15 – 4.15% |
Monel 400 | 63.0% min. | – | 2.5% max. | – | 28.0 – 34.0% | Carbon (C): ≤ 0.3% |
Hastelloy C276 | 57.0% min. | 14.5 – 16.5% | 4.0 – 7.0% | 15.0 – 17.0% | – | W: 3.0 – 4.5%, V: ≤ 0.35% |
Hastelloy C22 | 56.0% min. | 20.0 – 22.5% | 2.0 – 6.0% | 12.5 – 14.5% | – | W: 2.5 – 3.5%, C: ≤ 0.015% |
Alloy 20 | 32.0 – 38.0% | 19.0 – 21.0% | Bal. | 2.0 – 3.0% | 3.0 – 4.0% | Carbon (C): ≤ 0.06%, Nb: ≤ 1% |
Key Notes on Tables
- Custom Sizes: Beyond standard dimensions, manufacturers can produce pipes and tubes in specific sizes, lengths, and thicknesses to meet unique project requirements.
- Chemical Variability: Slight variations in chemical composition may occur depending on the manufacturer and specific requirements of a given ASTM standard.
Manufacturing Process of Nickel Alloy Seamless Pipe & Tube
The production of nickel alloy seamless pipes involves sophisticated techniques to ensure precise dimensions, superior mechanical properties, and defect-free surfaces. Here is a detailed step-by-step explanation:
Step 1: Raw Material Preparation
The process begins with the selection of high-quality nickel alloy billets. Each billet undergoes thorough inspection to ensure it meets chemical composition and mechanical property requirements.
- Inspection Procedures: X-ray fluorescence (XRF) and spectrometry are used to confirm material composition.
- Billet Dimensions: Typical billets are cylindrical with controlled sizes, ready for extrusion or piercing.
Step 2: Hot Extrusion Process
The billets are heated in a controlled furnace to temperatures between 1000°C to 1250°C, depending on the nickel alloy grade.
- Extrusion Techniques: A hydraulic press forces the billet through a die, creating a hollow tube shape.
- Wall Thickness Control: Adjusting the mandrel size during extrusion allows precise control over wall thickness.
Step 3: Piercing and Rolling
Rotary piercing is employed to form the seamless structure. A billet is rotated at high speed while a piercing tool creates the initial hole.
- Pilgering Process: The semi-finished tube is passed through pilger mills for further size reduction and precision shaping.
- Dimensional Accuracy: The rolling process ensures the pipe diameter remains uniform.
Step 4: Heat Treatment
Heat treatment enhances the mechanical properties and relieves stresses induced during extrusion and rolling.
- Annealing: The pipes are heated to a specific temperature and slowly cooled to improve ductility.
- Stress-Relieving: Ensures dimensional stability by eliminating internal stresses.
Step 5: Cold Drawing
Cold drawing achieves the exact dimensions and surface finishes required.
- Drawing Process: Pipes are pulled through a die at room temperature.
- Dimensional Tolerances: Achieves tighter tolerances and improved strength.
Step 6: Straightening and Sizing
Advanced straightening machines ensure pipes maintain perfect alignment and specified dimensions.
- Straightening Tools: Use rollers and clamps to remove curvature.
- Sizing Tolerances: Final adjustments are made to adhere to customer specifications.
Step 7: Surface Treatment
The pipes undergo surface polishing and cleaning to remove any scales or oxidation layers.
- Polishing Techniques: Electrolytic and mechanical polishing for a smooth finish.
- Coating Options: Anti-corrosion coatings are applied based on application needs.
Step 8: Non-Destructive Testing (NDT)
To ensure the pipes are free of defects, various NDT methods are employed:
- Ultrasonic Testing: Detects internal cracks.
- Eddy Current Testing: Identifies surface flaws.
- Dimensional Inspection: Verifies pipe diameter, thickness, and length.
Applications of Nickel Alloy Seamless Pipes & Tubes
1. Petrochemical Industry
Nickel alloys resist corrosive chemicals, making them ideal for reactors, distillation columns, and heat exchangers.
2. Aerospace
With excellent high-temperature strength, nickel alloy pipes are used in jet engines and exhaust systems.
3. Marine
Nickel alloys withstand saltwater corrosion, making them suitable for shipbuilding and offshore platforms.
4. How is the quality of nickel alloy seamless pipes ensured during manufacturing?
The quality is ensured through rigorous testing at every stage of production, including non-destructive testing methods such as ultrasonic, eddy current, and dimensional inspections. Additionally, raw materials are meticulously selected, and strict adherence to ASTM standards is maintained.
5. Are nickel alloy seamless pipes customizable?
Yes, nickel alloy seamless pipes can be customized based on specific requirements, including diameters, wall thicknesses, and lengths. Custom alloys, surface finishes, and protective coatings are also available for specialized applications.
6. What makes nickel alloy pipes suitable for high-temperature environments?
Nickel alloys exhibit excellent thermal stability, oxidation resistance, and mechanical strength at elevated temperatures, making them the material of choice for applications like turbines, heat exchangers, and high-pressure vessels.
Challenges in Manufacturing Nickel Alloy Seamless Pipes
The production of nickel alloy seamless pipes comes with unique challenges due to the complex nature of nickel-based materials and the need for precise manufacturing processes. Below are some of the critical hurdles faced:
1. Handling Material Strength at High Temperatures
Nickel alloys retain significant strength even at elevated temperatures, making them difficult to deform during extrusion, piercing, and cold drawing. High-temperature processes require advanced equipment and strict control over thermal conditions to prevent defects.
2. Preventing Surface Defects
Nickel alloys are prone to surface oxidation and scaling during heat treatment. Ensuring a high-quality surface finish requires the implementation of specialized cleaning and polishing techniques. Additional measures, such as controlled atmospheric heat treatments, are often needed.
3. Maintaining Dimensional Precision
Seamless pipes need to meet exact specifications for outside diameter, wall thickness, and length. Achieving these dimensions while avoiding wall thickness variations is challenging, particularly during hot extrusion and cold drawing stages.
4. Cost of Raw Materials
Nickel and nickel-based alloys are expensive compared to other metals. Ensuring optimal use of raw materials and minimizing waste during manufacturing is essential to keep costs under control.
5. Testing and Quality Control
The rigorous testing protocols, including non-destructive testing and dimensional inspections, add to the complexity of manufacturing. Ensuring the pipe meets both customer and international standards is labor-intensive and time-consuming.
Future Trends in Nickel Alloy Pipe Production
As industries evolve, the demand for more advanced nickel alloy seamless pipes and tubes continues to grow. Here are some key trends shaping the future of manufacturing:
1. Development of Advanced Alloys
Research and development efforts are focused on creating new nickel-based alloys with enhanced properties, such as increased resistance to corrosion, oxidation, and higher temperatures. These alloys will cater to the growing demands of specialized applications in aerospace, energy, and chemical processing.
2. Automation and Smart Manufacturing
The integration of automation and Industry 4.0 technologies is revolutionizing seamless pipe manufacturing. Automated extrusion and pilgering machines, coupled with real-time monitoring systems, improve production efficiency and reduce the likelihood of defects.
3. Sustainability Initiatives
With the global push toward sustainability, manufacturers are exploring eco-friendly production methods, such as recycling nickel alloys and using cleaner energy sources in manufacturing plants. The focus is on reducing the carbon footprint of nickel alloy pipe production.
4. Additive Manufacturing (3D Printing)
Although still in its infancy for seamless pipes, additive manufacturing is being explored as a potential method for producing customized nickel alloy components with intricate designs. This could open up new possibilities for reducing production waste and lead times.
5. Enhanced Testing Technologies
The development of advanced non-destructive testing (NDT) methods, such as phased-array ultrasonic testing (PAUT) and infrared thermography, will ensure even higher levels of quality control in seamless pipe production.
Comparison Between Nickel Alloy Seamless and Welded Pipes
While both seamless and welded pipes are used across various industries, their unique characteristics make them suitable for different applications. Here’s a detailed comparison:
Feature | Seamless Pipes | Welded Pipes |
---|---|---|
Strength | Higher strength due to the absence of weld seams | Moderate strength; weld seams can be a weak point |
Manufacturing Process | Produced through extrusion and piercing, no welding | Produced by rolling and welding flat plates |
Cost | More expensive due to complex production | Generally more cost-effective |
Applications | High-pressure and high-temperature systems | Low to medium pressure applications |
Size Availability | Limited to smaller sizes | Can be produced in larger diameters and lengths |
Durability | Superior durability in extreme conditions | May require additional reinforcements |
Applications of Nickel Alloy Seamless Pipes & Tubes
Nickel alloy seamless pipes and tubes are indispensable in industries requiring superior performance under harsh conditions. Here are some of the prominent applications:
1. Petrochemical and Chemical Processing
In petrochemical and chemical plants, seamless nickel alloy pipes are used in:
- Heat exchangers for transferring heat between chemical substances.
- Reactor vessels exposed to corrosive chemicals.
- Piping systems for the transportation of acids, alkalis, and other reactive substances.
2. Power Generation
Nickel alloy pipes are critical components in power plants, including:
- Steam turbines where they endure high temperatures and pressures.
- Boilers and condensers in thermal power generation.
- Heat recovery systems in renewable energy projects.
3. Aerospace Industry
In aerospace applications, nickel alloys provide the strength and heat resistance needed for:
- Jet engine components, such as exhaust ducts and turbine blades.
- Aircraft fuel systems, requiring corrosion resistance and high tensile strength.
4. Marine Industry
Seamless nickel alloy pipes withstand the challenges of seawater environments, making them suitable for:
- Offshore oil and gas platforms.
- Shipbuilding for piping and cooling systems.
- Desalination plants converting seawater into potable water.
5. Medical and Pharmaceutical Industries
The biocompatibility and corrosion resistance of nickel alloys make them ideal for:
- Medical equipment such as surgical tools and implants.
- Pharmaceutical processing equipment exposed to reactive chemicals.
Maintenance and Longevity of Nickel Alloy Seamless Pipes
Proper maintenance plays a crucial role in ensuring the durability and performance of nickel alloy seamless pipes. Given their application in extreme environments, implementing a maintenance strategy not only prolongs their lifespan but also prevents unexpected failures.
1. Inspection and Testing
Regular inspection and non-destructive testing are vital to identify defects or wear early.
- Visual Inspection: Check for surface defects like scratches, pitting, or corrosion.
- Ultrasonic Testing: Used to identify internal flaws without damaging the pipe.
- Eddy Current Testing: Detects surface cracks and thickness variations.
Frequency: Inspections should be scheduled quarterly for high-stress systems or annually for low-stress applications.
2. Cleaning Procedures
Cleaning nickel alloy pipes removes residues that could lead to corrosion or fouling.
- Chemical Cleaning: Use of acid or alkaline solutions to remove deposits, especially in chemical processing systems.
- Mechanical Cleaning: Use of brushes or pigging tools to remove internal build-ups in long pipelines.
- Steam Cleaning: Ideal for pipes in food and pharmaceutical industries, as it ensures sterilization.
Precaution: Avoid using cleaning agents containing chlorine, as they can cause stress corrosion cracking in nickel alloys.
3. Coating and Protection
Applying protective coatings or using surface treatments can prevent external corrosion.
- Anti-Corrosion Coatings: Protect the pipe from harsh external environments, especially in marine or coastal applications.
- Passivation: Enhances the natural oxide layer of nickel alloys to improve corrosion resistance.
- Protective Wrappings: For pipes exposed to high humidity or buried underground.
4. Stress and Pressure Monitoring
In high-pressure systems, stress monitoring prevents fatigue and deformation.
- Pressure Gauges: Monitor for pressure surges that can overstress the pipe.
- Thermal Monitoring: Ensures pipes are not exposed to temperatures exceeding their rated capacity.
- Vibration Analysis: Helps detect fatigue points in vibrating systems, such as in machinery or ship engines.
5. Preventive Maintenance Programs
Implementing a structured preventive maintenance plan ensures consistent performance:
- Replacement of Worn Components: Sections showing significant wear should be replaced immediately to avoid system failures.
- Routine Lubrication: For moving parts or connections in pipe systems.
- System Flushing: Prevents blockages caused by sediment or chemical buildup.
Benefits of Regular Maintenance
- Increased Lifespan: Regular care extends the operational life of nickel alloy pipes.
- Improved Safety: Prevents catastrophic failures in critical systems.
- Cost Efficiency: Reduces the need for frequent replacements or emergency repairs.
Conclusion
The seamless integration of cutting-edge technology, stringent manufacturing standards, and a commitment to quality makes nickel alloy seamless pipes a cornerstone of modern industry. From their high resistance to corrosion and extreme temperatures to their adaptability in specialized applications, these pipes are unparalleled in performance.
Through detailed manufacturing processes, rigorous testing, and proper maintenance, nickel alloy seamless pipes provide long-term reliability and safety in some of the harshest operational environments. As industries evolve and demand even greater performance, the future of nickel alloy pipe production promises further innovation, sustainability, and precision.
You must be logged in to post a comment.