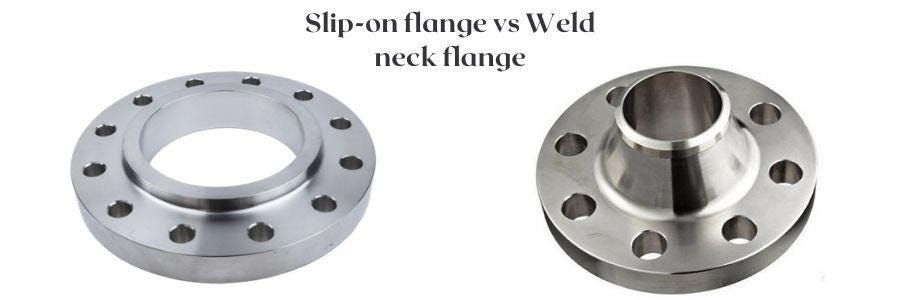
Difference Between Weld Neck Flange and Slip-On Flange
Introduction
Flanges are essential components in piping systems, serving as connectors for pipes, valves, pumps, and other equipment. Among the various types of flanges, weld neck flanges and slip-on flanges are two of the most commonly used. Each has distinct characteristics, advantages, and applications. In this comprehensive exploration, we’ll delve into the differences between these two flange types, examining their design, installation, performance, and suitability for different applications.
1. Design and Structure
Weld Neck Flange
- Shape and Structure: A weld neck flange is characterized by a long, tapered hub that gradually transitions from the flange body to the pipe. This design helps distribute stress evenly, reducing the risk of deformation or failure.
- Bore Size: The bore of a weld neck flange matches the inner diameter of the connecting pipe, ensuring a smooth flow of fluids and reducing turbulence.
- Material: Weld neck flanges are typically made from materials like carbon steel, stainless steel, or alloy steel, chosen based on the application’s pressure, temperature, and corrosion resistance requirements.
Slip-On Flange
- Shape and Structure: A slip-on flange has a flat face and a bore slightly larger than the outer diameter of the pipe. This allows the flange to slip over the pipe before welding.
- Bore Size: The bore of a slip-on flange is larger than the pipe’s outer diameter, which facilitates easy alignment and installation.
- Material: Like weld neck flanges, slip-on flanges are made from various materials, including carbon steel, stainless steel, and alloy steel, selected based on the specific application needs.
2. Installation Process
Weld Neck Flange
- Welding Method: The installation of a weld neck flange involves butt-welding the flange to the pipe. This requires precise alignment and skilled welding to ensure a strong, leak-proof joint.
- Preparation: The pipe end and flange must be prepared with a beveled edge to facilitate the welding process. Proper fit-up and alignment are crucial to achieving a high-quality weld.
- Inspection: After welding, the joint is typically inspected using non-destructive testing methods like radiography or ultrasonic testing to ensure its integrity.
Slip-On Flange
- Welding Method: A slip-on flange is installed by slipping it over the pipe and then performing fillet welds on both the inside and outside of the flange. This process is generally simpler and quicker than butt-welding.
- Preparation: Minimal preparation is required for slip-on flanges, as they do not require beveled edges. The pipe end is simply inserted into the flange bore.
- Inspection: Visual inspection is often sufficient for slip-on flange welds, although additional testing may be conducted for critical applications.
3. Performance and Stress Distribution
Weld Neck Flange
- Stress Distribution: The tapered hub of a weld neck flange provides excellent stress distribution, reducing the risk of localized stress concentrations. This makes weld neck flanges ideal for high-pressure and high-temperature applications.
- Leak Prevention: The butt-welded joint offers superior leak prevention, making weld neck flanges suitable for critical applications where leakage could have severe consequences.
- Durability: Weld neck flanges are known for their durability and ability to withstand harsh operating conditions, including thermal cycling and vibration.
Slip-On Flange
- Stress Distribution: Slip-on flanges have less effective stress distribution compared to weld neck flanges. The fillet welds can create stress concentrations, making them less suitable for high-pressure applications.
- Leak Prevention: While slip-on flanges provide a reliable seal for many applications, the potential for leaks is higher than with weld neck flanges, especially under high-pressure conditions.
- Durability: Slip-on flanges are generally less durable than weld neck flanges, particularly in demanding environments. However, they are adequate for low to moderate pressure and temperature applications.
4. Cost and Application Suitability
Weld Neck Flange
- Cost: Weld neck flanges are typically more expensive than slip-on flanges due to their complex design and the skilled labor required for installation. The cost is justified by their superior performance in critical applications.
- Application Suitability: Weld neck flanges are ideal for high-pressure, high-temperature, and high-stress applications, such as in the oil and gas, petrochemical, and power generation industries.
Slip-On Flange
- Cost: Slip-on flanges are generally more cost-effective than weld neck flanges, both in terms of initial purchase price and installation costs. Their simpler design and installation process contribute to lower overall costs.
- Application Suitability: Slip-on flanges are suitable for low to moderate pressure and temperature applications, such as in water distribution, HVAC systems, and general industrial use.
5. Advantages and Disadvantages
Weld Neck Flange
- Advantages:
- Excellent stress distribution and leak prevention.
- High durability and reliability in demanding conditions.
- Suitable for critical applications with stringent safety requirements.
- Disadvantages:
- Higher cost and more complex installation process.
- Requires skilled labor and precise alignment.
Slip-On Flange
- Advantages:
- Lower cost and simpler installation process.
- Adequate performance for many general-purpose applications.
- Easier to align and install, reducing labor costs.
- Disadvantages:
- Less effective stress distribution and higher potential for leaks.
- Not suitable for high-pressure or high-temperature applications.
Conclusion
In summary, both weld neck flanges and slip-on flanges have their unique characteristics, advantages, and applications. The choice between the two depends on the specific requirements of the piping system, including pressure, temperature, stress, and budget considerations. Weld neck flanges offer superior performance for critical applications, while slip-on flanges provide a cost-effective solution for less demanding environments. Understanding these differences is essential for selecting the right flange type to ensure the safety, reliability, and efficiency of your piping system.
You must be logged in to post a comment.