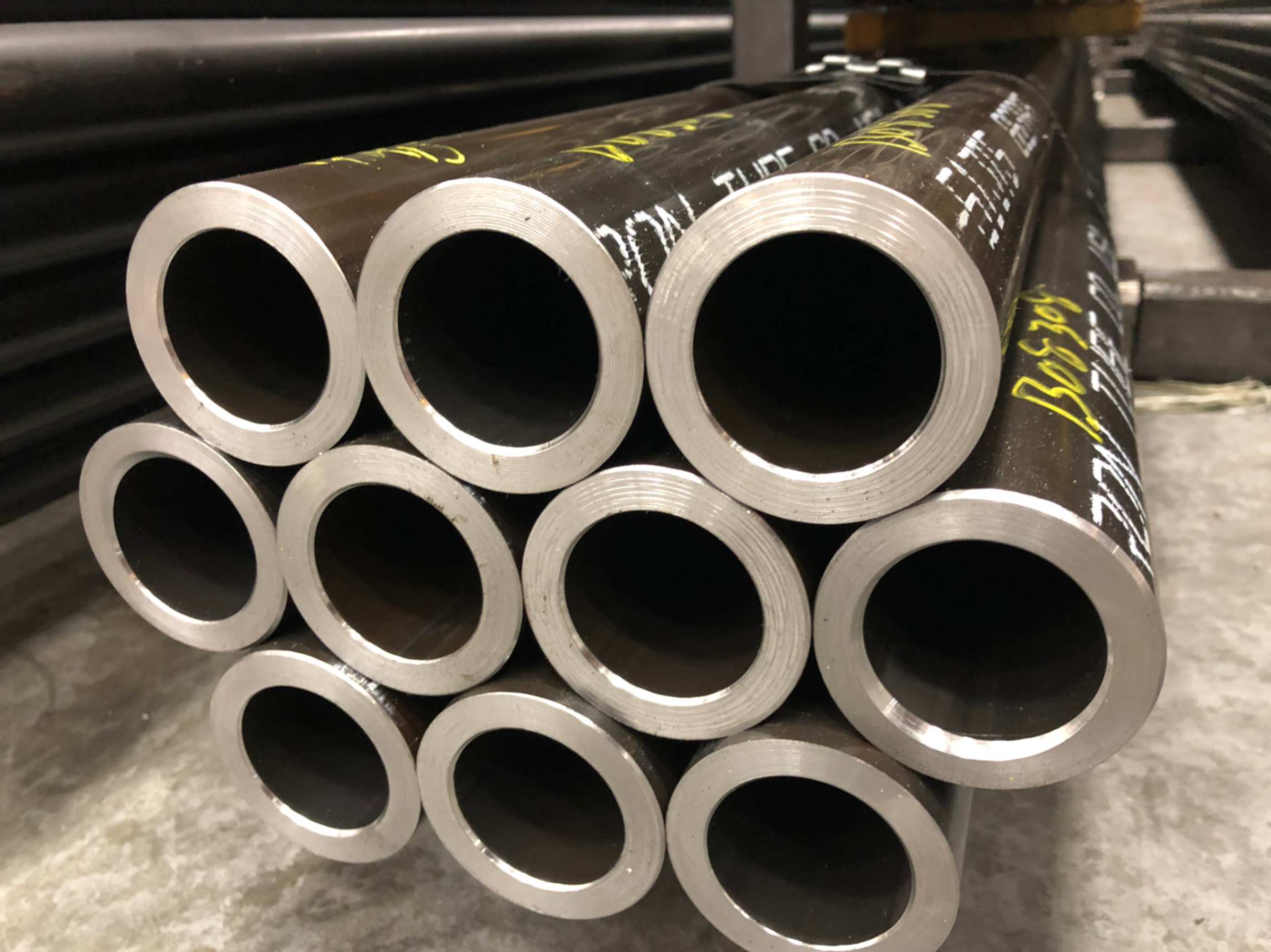
Outline for the Article on Drawn Over Mandrel Tubing (DOM Steel Pipe)
Main Heading | Subheadings |
---|---|
Introduction | What is Drawn Over Mandrel (DOM) Tubing? |
Why DOM Tubing is Widely Used in Industrial Applications | |
Key Features of DOM Steel Pipes | |
Manufacturing Process of DOM Tubing | What is the DOM Process? |
Steps in the DOM Manufacturing Process | |
Difference Between DOM and ERW Tubing | |
Material Grades Used in DOM Tubing | Common Grades: A513 Type 5, 1018, 1020, 1026 |
Chemical Composition of DOM Steel | |
Mechanical Properties of DOM Tubes | |
Features and Benefits of DOM Tubing | Seamless Inner Surface |
High Dimensional Accuracy | |
Excellent Weldability and Machinability | |
Superior Strength and Durability | |
Applications of DOM Steel Tubing | Automotive and Motorsport Applications |
Structural and Mechanical Engineering | |
Industrial and Hydraulic Systems | |
Construction and Furniture Manufacturing | |
Advantages of DOM Tubing | High Strength-to-Weight Ratio |
Smooth Inner Surface for Fluid and Gas Flow | |
Tight Dimensional Tolerances | |
Cost-Effectiveness in Precision Applications | |
Comparison of DOM Tubing with Other Types of Steel Tubing | DOM Tubing vs. Seamless Steel Pipes |
DOM Tubing vs. Electric Resistance Welded (ERW) Pipes | |
DOM Tubing vs. Cold Drawn Seamless Tubing | |
Standard Dimensions and Sizes of DOM Tubing | Outer Diameter (OD) and Wall Thickness |
Available Sizes and Custom Options | |
Dimensional Tolerances | |
Heat Treatment and Surface Finishes | Heat Treatment Methods: Normalizing, Annealing, Quenching, Tempering |
Surface Finishes: Black, Pickled, Polished | |
Coating Options for Corrosion Resistance | |
Quality Control and Testing | Non-Destructive Testing (NDT) for Welds and Surface Quality |
Dimensional Inspections and Surface Finish Checks | |
Certification and Compliance | |
Sourcing and Availability | Leading Manufacturers and Suppliers of DOM Tubing |
Market Availability of Standard Sizes | |
Custom Manufacturing Options for DOM Tubes | |
Cost and Value Proposition | Factors Affecting the Cost of DOM Tubing |
Cost Comparison of DOM vs. Seamless and ERW Tubing | |
Long-Term Value of DOM Tubes in Industrial Applications | |
FAQs | What is the Difference Between DOM and ERW Tubing? |
Can DOM Tubing Be Used in High-Pressure Applications? | |
What Are the Typical Sizes of DOM Tubing? | |
How is DOM Tubing Heat Treated? | |
Is DOM Tubing Suitable for Hydraulic Systems? | |
What is the Lifespan of DOM Tubing in Industrial Applications? | |
Conclusion | Summary of DOM Tubing Features and Applications |
Why DOM Tubing is the Best Choice for Precision and High-Stress Applications | |
Final Recommendations |
Drawn Over Mandrel Tubing (DOM Steel Pipe)
Drawn Over Mandrel (DOM) tubing is a high-strength, precision steel pipe widely used in industrial applications requiring seamless construction, dimensional accuracy, and superior strength. DOM tubing is the result of a specialized manufacturing process that improves the mechanical properties of steel tubing and creates a smooth, seamless inner surface. This article explores the features, manufacturing process, benefits, and applications of DOM tubing in detail.
Introduction
What is Drawn Over Mandrel (DOM) Tubing?
DOM tubing is a type of cold-drawn electric resistance welded (ERW) steel pipe that undergoes a secondary process to enhance its strength, dimensional accuracy, and surface finish. During the DOM process, the tubing is drawn through a die and over a mandrel, which eliminates weld seams, refines the grain structure, and ensures tight tolerances.
Why DOM Tubing is Widely Used in Industrial Applications
- High Strength-to-Weight Ratio: DOM tubing is lightweight but incredibly strong, making it suitable for load-bearing and high-stress applications.
- Dimensional Precision: Tight tolerances ensure reliability in applications requiring accurate fits.
- Seamless Interior Surface: A smooth bore improves fluid flow and minimizes friction in hydraulic and pneumatic systems.
Key Features of DOM Steel Pipes
- Seamless-Like Construction: While technically not seamless, DOM tubing offers mechanical properties and a surface finish comparable to true seamless pipes.
- Improved Tensile Strength: The cold-drawing process increases the pipe’s strength.
- Versatility: Widely used in industries such as automotive, construction, and machinery manufacturing.
Manufacturing Process of DOM Tubing
What is the DOM Process?
The Drawn Over Mandrel (DOM) process is a secondary manufacturing step performed on electric resistance welded (ERW) tubing. It involves pulling the tubing through a die and over a mandrel, refining its dimensional tolerances, surface quality, and mechanical properties.
Steps in the DOM Manufacturing Process
- Initial Formation: Steel is rolled into a cylindrical shape and welded along its seam using the ERW process.
- Cold Drawing:
- The welded tube is pulled through a die while being supported internally by a mandrel.
- This step refines the tube’s outer diameter (OD), wall thickness, and straightness.
- Heat Treatment: Post-drawing, the tube is heat-treated to relieve stress, improve ductility, and refine grain structure.
- Surface Finishing: The pipe undergoes polishing or pickling for a smooth surface.
Difference Between DOM and ERW Tubing
Feature | DOM Tubing | ERW Tubing |
---|---|---|
Manufacturing | Secondary cold-drawing process | Welded with no further refinement |
Surface Finish | Seamless-like, smooth | Visible weld seam |
Strength | Higher | Moderate |
Applications | Precision and high-stress | General-purpose |
Material Grades Used in DOM Tubing
Common Grades
DOM tubing is often made from low-carbon and alloy steels. Common grades include:
- A513 Type 5: A widely used DOM grade with excellent mechanical properties.
- 1018 and 1020: Low-carbon steels known for their machinability and weldability.
- 1026: A stronger option with better tensile and yield strength.
Chemical Composition of DOM Steel
Element | 1018 | 1020 | 1026 |
---|---|---|---|
Carbon (C) | 0.14–0.20% | 0.18–0.23% | 0.22–0.28% |
Manganese (Mn) | 0.60–0.90% | 0.30–0.60% | 0.60–0.90% |
Phosphorus (P) | ≤ 0.04% | ≤ 0.04% | ≤ 0.04% |
Sulfur (S) | ≤ 0.05% | ≤ 0.05% | ≤ 0.05% |
Mechanical Properties of DOM Tubes
Property | A513 Type 5 | 1018 Steel | 1026 Steel |
---|---|---|---|
Tensile Strength | 490–620 MPa | 440–600 MPa | 600–700 MPa |
Yield Strength | 365 MPa | 370 MPa | 500 MPa |
Elongation (%) | ≥ 15% | ≥ 15% | ≥ 10% |
Applications of DOM Steel Tubing
DOM tubing’s superior strength, precision, and smooth surface finish make it an indispensable component across a variety of industries. Below are the key applications where DOM steel tubing excels:
1. Automotive and Motorsport Applications
DOM tubing is widely used in the automotive and motorsport sectors due to its high strength-to-weight ratio and seamless construction. Key applications include:
- Roll Cages: Protect drivers in high-speed accidents by absorbing and distributing impact energy effectively.
- Driveshafts: DOM tubes are used for driveshafts because they provide excellent torsional strength and durability.
- Suspension Components: DOM tubing is employed in control arms, stabilizer bars, and other suspension parts that experience high stresses.
- Exhaust Systems: The smooth surface finish allows for efficient airflow and reduced friction, improving engine performance.
Why DOM Tubing is Ideal for Automotive Use:
- Lightweight yet strong, reducing the overall weight of vehicles.
- High dimensional accuracy ensures a perfect fit in precision applications.
2. Structural and Mechanical Engineering
In structural and mechanical engineering, DOM tubing is preferred for its strength and tight tolerances. Common applications include:
- Support Structures: Used in load-bearing frameworks for industrial equipment and buildings.
- Mechanical Linkages: Ideal for machine components that need to transmit motion under high stress.
- Robotics: Precision and strength make DOM tubing suitable for robotic arms and frames.
Advantages:
- Withstands high mechanical loads without deformation.
- Seamless construction ensures consistent performance under stress.
3. Industrial and Hydraulic Systems
DOM tubing plays a crucial role in hydraulic and pneumatic systems, where internal fluid flow efficiency and pressure resistance are critical. Applications include:
- Hydraulic Cylinders: Used in hydraulic systems for construction and manufacturing equipment, DOM tubing ensures durability and resistance to internal pressure.
- Pneumatic Tubes: DOM’s smooth inner bore minimizes turbulence and maximizes airflow efficiency.
- Drill Rods: Frequently used in industrial drilling applications for their toughness and ability to handle bending and rotational stresses.
Benefits in Hydraulic Systems:
- Seamless inner bore reduces the risk of leaks and improves fluid dynamics.
- Withstands high internal pressures and cyclic loads.
4. Construction and Furniture Manufacturing
DOM tubing is also popular in the construction and furniture industries for its aesthetic appeal, lightweight structure, and ease of fabrication. Applications include:
- Scaffolding: Used in high-strength scaffolding systems for construction sites.
- Furniture Frames: Frequently used in the production of chairs, tables, and modular furniture for its smooth surface and uniform appearance.
- Handrails and Railings: Provides both strength and a clean look in architectural projects.
Why DOM Tubing is Preferred:
- High machinability allows for custom shapes and designs.
- Smooth surface finish requires minimal polishing for aesthetic purposes.
Advantages of DOM Tubing
DOM tubing offers several unique advantages over other types of steel tubing:
1. High Strength-to-Weight Ratio
DOM tubing is lightweight while providing superior strength, making it an excellent choice for industries such as aerospace, automotive, and motorsports. Its strength-to-weight ratio allows for efficient use of material without compromising safety or performance.
2. Smooth Inner Surface
The DOM process creates a seamless, polished inner surface, which is critical for applications like hydraulic cylinders and pneumatic tubes where fluid flow efficiency is paramount. The lack of weld seams minimizes friction and prevents weak points that could lead to leaks or failure.
3. Tight Dimensional Tolerances
DOM tubing offers exceptional dimensional precision in terms of outer diameter, inner diameter, and wall thickness. This makes it the preferred choice for applications requiring exact fits, such as precision machinery and automotive components.
4. Superior Durability and Fatigue Resistance
The cold-drawing process refines the grain structure of the steel, enhancing its durability and resistance to fatigue. This makes DOM tubing ideal for high-stress and high-impact applications.
5. Cost-Effectiveness in Precision Applications
Although DOM tubing is more expensive than standard ERW tubing, it provides better long-term value due to its superior performance, reduced maintenance needs, and extended lifespan. It offers a cost-effective solution for industries requiring precision and strength.
Comparison of DOM Tubing with Other Types of Steel Tubing
DOM Tubing vs. Seamless Steel Pipes
Feature | DOM Tubing | Seamless Steel Pipes |
---|---|---|
Manufacturing Process | Cold-drawn over a mandrel | Made from pierced billets |
Surface Finish | Polished, smooth | Rougher interior and exterior |
Strength | High | Very high |
Cost | Moderate | Higher |
Applications | Precision, hydraulic systems | High-pressure and temperature systems |
DOM Tubing vs. ERW Pipes
Feature | DOM Tubing | ERW Pipes |
---|---|---|
Seam | Seamless-like | Weld seam visible |
Strength | Higher | Moderate |
Surface Finish | Smooth | Standard |
Applications | Precision applications | General-purpose use |
DOM Tubing vs. Cold Drawn Seamless Tubing
Feature | DOM Tubing | Cold Drawn Seamless |
---|---|---|
Cost | Lower | Higher |
Surface Finish | Comparable | Polished |
Strength | Comparable | Very high |
Applications | Precision, moderate stress | Extreme pressure or temperature |
Standard Dimensions and Sizes of DOM Tubing
Outer Diameter (OD) and Wall Thickness
DOM tubing is available in a wide range of sizes:
Outer Diameter (OD) | Wall Thickness |
---|---|
10 mm – 300 mm | 0.5 mm – 25 mm |
Available Sizes and Custom Options
DOM tubing can be customized for specific applications. Common lengths include 6 meters or custom cut-to-length options. Tolerances can be further refined based on project needs.
Dimensional Tolerances
Dimension | Tolerance |
---|---|
Outer Diameter | ±0.5% |
Wall Thickness | ±10% |
Straightness | 1/16 inch per 3 feet |
FAQs
1. What is the Difference Between DOM and ERW Tubing?
DOM tubing undergoes a secondary drawing process that eliminates weld seams and improves strength, precision, and surface finish, whereas ERW tubing retains visible weld seams and has lower mechanical properties.
2. Can DOM Tubing Be Used in High-Pressure Applications?
Yes, DOM tubing is suitable for moderate-pressure hydraulic and pneumatic systems due to its seamless-like construction and high strength.
3. What Are the Typical Sizes of DOM Tubing?
DOM tubing is available in sizes ranging from 10 mm to 300 mm outer diameter, with wall thicknesses from 0.5 mm to 25 mm.
4. How is DOM Tubing Heat Treated?
DOM tubing can be heat-treated through normalizing, annealing, or quenching and tempering to enhance its mechanical properties for specific applications.
5. Is DOM Tubing Suitable for Hydraulic Systems?
Yes, DOM tubing is ideal for hydraulic systems due to its smooth inner surface, which reduces friction and ensures efficient fluid flow.
Conclusion
DOM (Drawn Over Mandrel) tubing is a superior option for applications requiring strength, precision, and a seamless-like finish. Its high dimensional accuracy, excellent machinability, and durability make it indispensable in industries like automotive, construction, and industrial hydraulics. While more expensive than standard ERW tubing, its performance and long-term value justify the cost in precision and high-stress applications.
By choosing DOM tubing for critical applications, industries can ensure reliable performance, reduced maintenance, and enhanced operational efficiency.
You must be logged in to post a comment.